技術情報溶接Q&A
F002高速すみ肉ガスシールドアーク溶接法(HS-MAG法)について
1. はじめに
水平すみ肉継手の比率の高い造船、橋梁分野では、溶接のトータルコスト低減のために、溶接の高速化省人化が要求されております。近年その良好な溶接作業性、高溶着性、経済性等の特長から、フラックス入りワイヤを用いる水平すみ肉溶接の自動化で大幅に普及していますが、高速化するほどアンダーカットの発生や凸ビードになるなどビード形成性が劣化すること、また造船、橋梁等ではプライマー塗装が前提であり、ピット、ブローホール対策からも現状では60~70cm/min程度が上限速度となっています。以上の背景から、弊社では、専用シームレスフラックス入リワイヤを用いる2電極1プール高速水平すみ肉溶接法(HS-MAG法)を開発しました。本法は溶接速度1.2~1.5m/minで脚長5~6mmの良好な水平すみ肉ビードが得られます。以下にHS-MAG法の特徴及び性能例について紹介します。
2. HS-MAG法の原理・特徴
水平すみ肉溶接の高速化には、必要脚長に見合う溶着金属量が必要になるので、必然的に高速化するほど高電流溶接となります。この場合アンダーカットの発生や凸ビードになるなど、ビード形成に間題点が生じます。高速溶接で問題になるアンダーカットの発生原因は次のように考えられています。
① 高速溶接は図1の概念図に示す様こ、ビード止端部の凝固位置(Xs)が前進し、溶融プールの後退距離(Xm)を大きくします。アンダーカットはXmとXsの相対的位置関係により決まり、Xs<Xmの時アンダーカットが発生します。従って、アンダーカットのない良好なビード形成には、アークにより溶融された溶込み面に溶融金属が満たされビード止端部凝固開始位置に個体露出面が発生しない溶接条件を選定する必要があります。
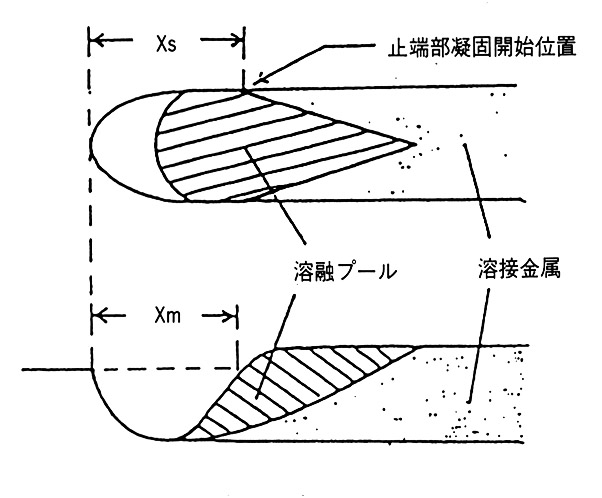
図1
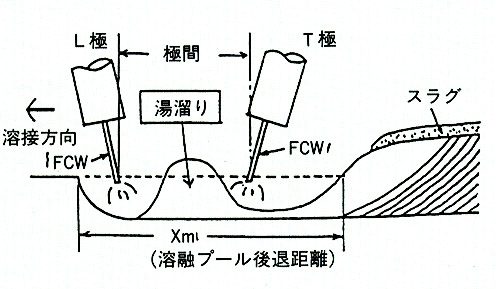
図2
(1)2電極配置により、熱源を分散させかつ電極間に「湯溜り」を形成させることにより、アーク力及び溶融プールの後退を抑制 しアンダーカットを防止する。
(2)フラックス入リワイヤの生成スラグによりビード形成能を向上させる。また、フラックス入リワイヤは高溶着性なので、相対的に低入力化でき高速化に有効である。
(3)耐プライマー性良好な専用SFワイヤ(SF-1F、SM-1F、1.6mmΦ)との組合せにより、無機ジンクプライマー塗装鋼板のすみ肉溶接でピット等の欠陥発生を抑制する。
以上の考え方に基づき開発したHS-MAG法の主な特徴は次の通りです。
① 専用SFワイヤによる2電極1プール水平すみ肉溶接です。
② 脚長5~6mmのすみ肉ビートが溶接速度1.2m/min以上で得られます。
③ ビード外観と形状が良好です。
④ 無機ジンクプライマー塗装鋼板の溶接で、優れた耐ピット性及び耐ブローホール性が得られます。
3. HS-MAG法の溶接性能
●3-1 溶接条件とビ-ド形成性HS-MAG法において、高速で良好なビ-ドを得るには、電極間に安定した「湯溜り」形成が必要で、それには適切な溶接条件を選定する必要があります。
① 溶着速度
例えば脚長5.5mmのビードを溶接速度1.2m/minで得るためには約170g/minの溶着量が必要であり(図3)、1電極では高電流を投与せざるを得ないためビード形状が劣化します。このため本法では2電極方式にして1電極当りの溶接電流を小さくして熱源の分散を図りました。ワイヤ径は電源容量及び溶接件範囲から1.6Φ×1.6Φの組合せとしました。
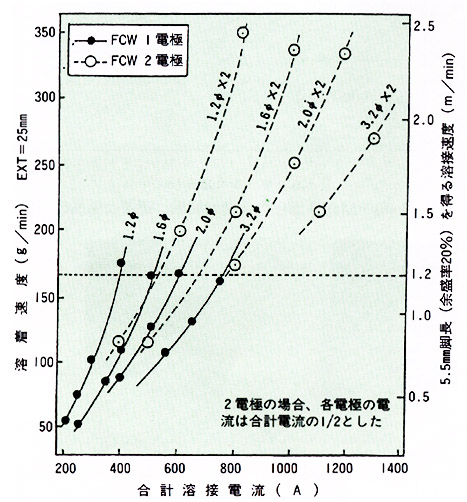
図3
② 極間距離
先行(L)と後行電極(T)の極間距離は、15~40mmの範囲が「湯溜り」が安定し、高速でも良好なビ-ドが得られます(表1)。
表1
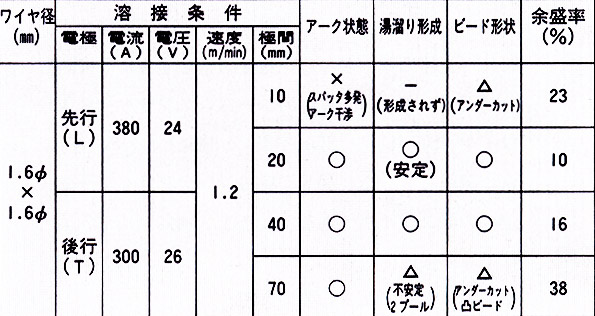
電源極牲の組合せは、アーク安定性及びビード形成性からDC(+)-DC(+)が最良です。
④ 溶接電流
電流配分はL極電流をT極電流よりも高めにした方が「湯溜り」が安定し、良好なビードが得られます。またビ-ド形状は電流が高いほど溶接速度の影響を受けやすいため、適正合計電流は1.6Φ×1.6Φで約550~850Aの範囲です(図4)。
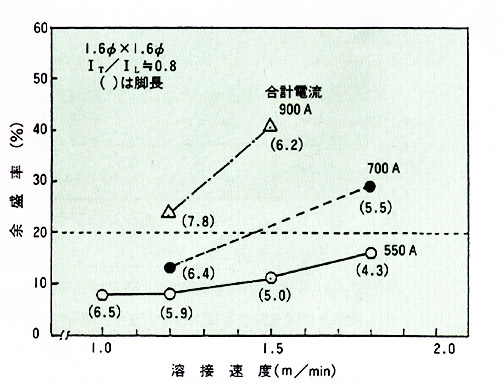
図4
⑤ 溶接電圧
L極の電圧をT極電圧より相対的に低くした方が溶融プールを後退させるアーク勢力圏を小さくできビ-ド形成に有利です。
⑥ 狙い位置
L極の狙い位置はコ-ナーから0~2mm、T極はL極から2~3mm手前が等脚性ビードが得られます。
●3-2 ショッププライマー対策
プライマー塗装鋼板の水平すみ肉溶接では、プライマー分解ガスに超因するピット、ガス溝等の欠陥が生じます。そこでフラックス入りワイヤの組成面から、これら欠陥に強くかつ高速溶接こ適合するよう検討した結果、水平すみ肉専用のシームレスフラックス入りワイヤ(SF-1F、SM-1F)を開発し、HS-MAG法に適用しました。図5こ無機ジンクプライマー塗装鋼板の耐プライマー性を示します。開発ワイヤの組合せでは溶接速度1.2m/minでピット、ガス溝が従来ワイヤより大幅に減少しています。
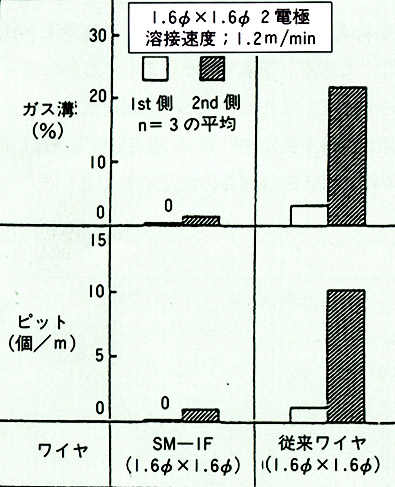
図 5
●3-3 適正溶接条件の一例
HS-MAG法の標準溶接条件の1例及びビード形状例を表2及び図6及び写真1に示します。本法では脚長5~6mmの水平すみ肉ビードが1.2m/min以上の溶接速度で得られ、1電極の2倍以上の高速化が達成できます。
表2
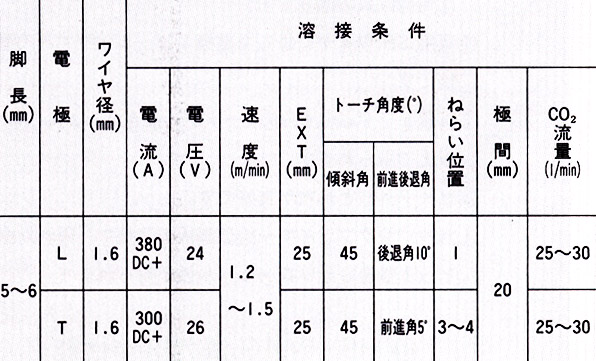
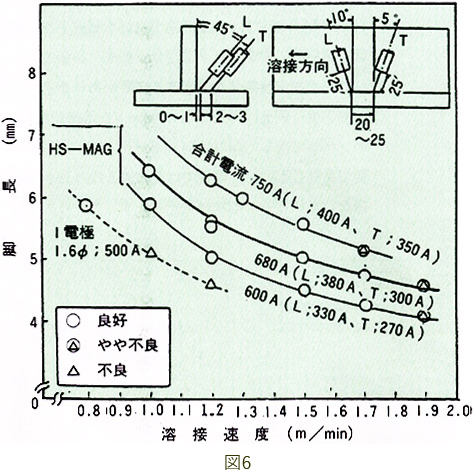
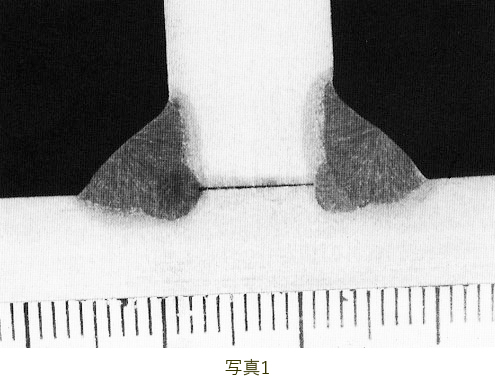
HS-MAG法の水平すみ肉溶接条件範囲をフラックス入りワイヤを使用する従来溶接法(1電極及び2電極2プール法)と比較して図7に示します。1電極溶接の場合、脚長が大きくなるほど限界速度が低速になり、標準の5~6mm脚長では約80cm/minです。一方極間距離を大きくした2電極2プール法では、溶融池が2つに分離するため個々の電極の限界速度は1電極の場合とほぼ同じです。2段ビードになるため、大脚長が得られやすいが、逆に6mm以下の小脚長が得られにくい問題があります。これに対しHS-MAG法は脚長範囲が4~7mmと広くなると共に、例えば脚長5mmの良好なビ-ドが1.5m/min以上の高速で得られ、従来法の約2倍の高速化が達成されます。
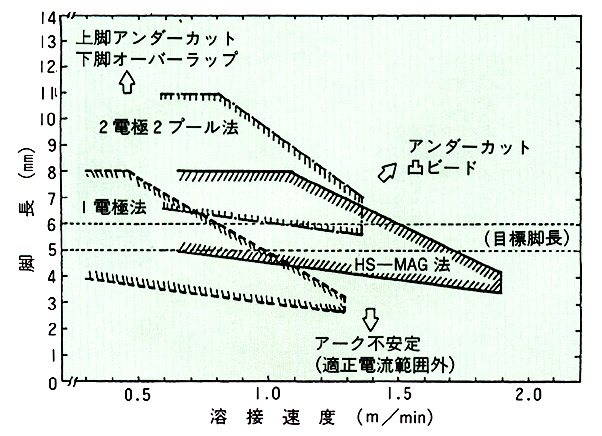
図 7
4. HS-MAG法の適用例
写真2は、造船のラインウェルダーによるロンジ先付溶接にHS-MAG法が適用されている状況を示したものです。これは、ロンジ材5本が同時溶接可能なツインタンデム方式20電極溶接装置の中核技術としてHS-MAG法を適用した1例であり、本溶接装置により、従来より大幅な高速化、高能率化を達成しています。この他、HS-MAG法は高速すみ肉溶接法として注目を集め、装置化も容易であることから、造船及び橋梁を中心に実用化されております。
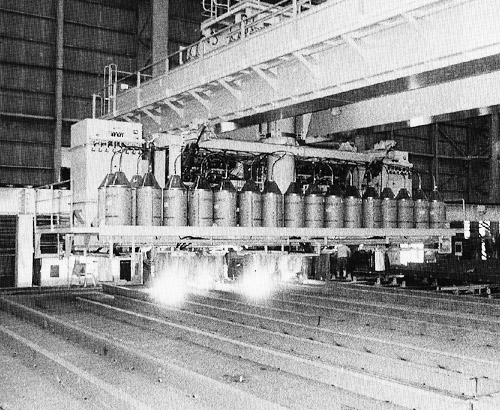
写真2
5. おわりに
溶接構造物の中で特に比率の高い水平すみ肉溶接について、その高速化を検討し、専用SFワイヤ(SF-1F、SM-1Fを用い電極間に「湯溜り」を安定形成することにより水平すみ肉溶接の高速化を可能とした新しい2電極1プール水平すみ肉CO₂溶接法(HS-MAG法)を開発しました。本法は無機ジンクプライマー鋼板を溶接速度1.2m/min以上の高速で水平すみ肉溶接することが可能であり、溶接の高速化、高能率化及びトータルコスト低減に貢献できるものと確信しています。〈参考文献〉
1)西ほか:高速サブマージアーク溶接法の研究(第1報);溶接学会誌Vol.51No.8(1982)