技術情報溶接Q&A
F003メタルコアードワイヤSM-1適用による
極厚ボックス柱の経済的制作について
1. はじめに
最近における我が国の鉄骨需要量は、一昨年後半から一層深刻の度を増したバブル経済崩壊の影響を受け、減少の兆しは見られるものの、一千万トンの大台には達すると思われます(図1)。これは、マンションやテナントビルなど中小物件の落ち込みに対し、主として大都市に建造される高層ビルなどの大型物件が堅調なことによるものと考えられます(図2)。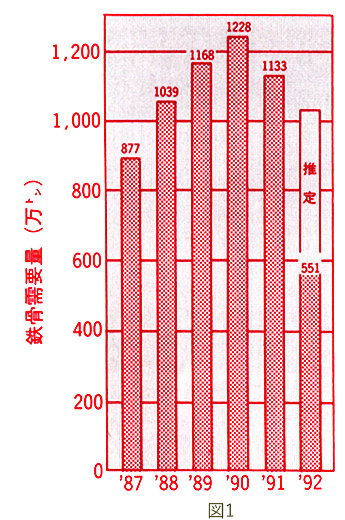
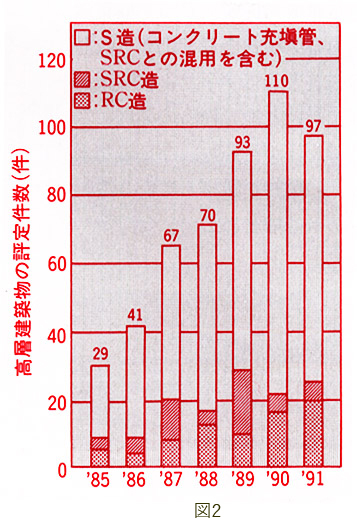
ところで、これら大型建築物は、近年超高層化と梁の大スパン化により、その使用鋼材が極厚化の傾向にあります。このことは、日本建築センター性能評定シートを(表1)見ると、柱の最大板厚において7mm以上である物件が、この1年間で10数件にも及ぶことから明らかです。
表1
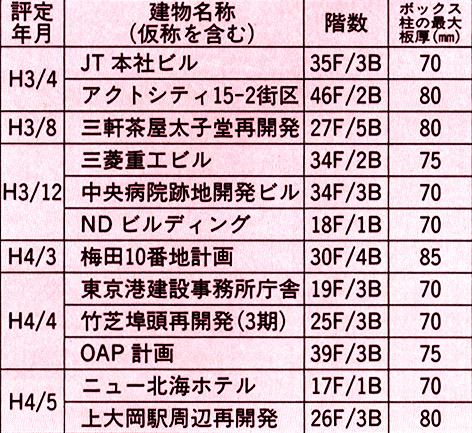
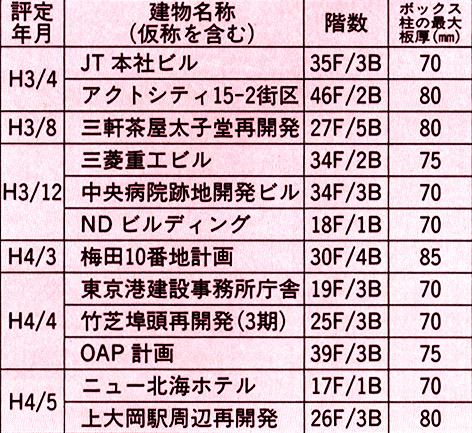
今回は、このような極厚ボックス柱製作に適用されている溶接法を整理するとともに、大入熱サブマージアーク溶接(以下SAW)の下盛りにCO₂溶接用メタルコアードワイヤ(以下MCW)が実用されている例を紹介し、関係各位のご参考に供したいと思います。
2. ボックス柱のかど継手溶接法について
(1)溶接法の種類現在、実用に供されているボックス柱かど継手のフルペネ部に対する溶接法を表2に、板厚毎の適応溶接法を表3に示します。これら溶接法のうち、1層SAW法は最も高能率であるため、広く活用されています。また、ボックス柱の過半数を占める板厚50~55mmまでに対しては、2電極1層SAW法が確立されています。最近では、これ以上の板厚に対する2電極1層SAW法の適用拡大や3電極1層SAW法による極厚柱の溶接が鋭意検討されています。
表2
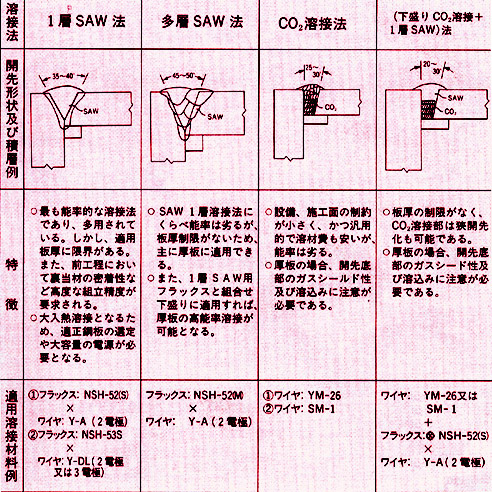
表3
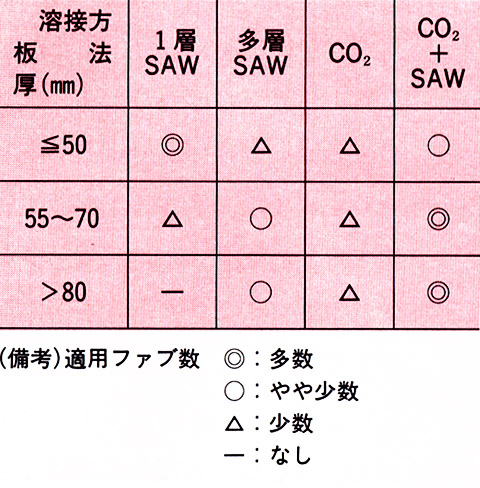
板厚の増加傾向にあって、現有設備を有効利用するには、開先上部に1層SAW可能な溶接断面積を残すよう、CO₂溶接にて下盛りするのが最も経済的であると考えられます。これまで、この方法を採用することにより板厚100mmまでの溶接実績があります。この場合には、特に開先底部に発生しやすい融合不良や気孔などの欠陥を防止するため、適正溶接条件の選定とガスシールド効果を高めるノズル形状の検討が必要です。
(2)(下盛リCO₂溶接+1層SAW)法
CO₂溶接による下盛り法は、フルペネ部とパーシャルペネ部を連続的にSAW仕上げするため、従来からフルペネ箇所に適用されてきました。この利点は多層SAW法にくらべ、
①開先を狭くできる、
②アークタイム率を向上できる、
③溶材費が安く抑えられるなどがあります。
また、この下盛りCO₂溶接には一般に1.6Φのソリッドワイヤが使用されます。しかし、最近では太径MCWにより
①溶着速度の向上、
②スパッタ量の減少や
③融合不良などの欠陥防止が可能になってきました。
これは、近年に至り性能の優れたMCWが開発されたことによるといっても過言ではありません。図3.1・3.2・3.3は弊社のMCWであるSM-1とソリッドワイヤ(YGW-11)間における溶接能率及びスパッタ発生量を比較したものです。ソリッドワイヤにくらべ、特にSM-1の溶着速度は早く、スパッタ量の少ないことは注目に値します。さらに、SM-1はアークが安定、かつ拡がるため、高電流溶接にも拘わらず溶込み形状が理想的であります。このことは、これまでソリッドワイヤにて時々見られる梨の実状割れや融合不良などの溶接欠焔に対し優利となっています。図4は、ボックス柱フルペネ部の長さを2mと考え、この箇所において1層SAWで仕上げられる最大断面480mm²を残すよう、1.6Φのソリッドワイヤと2.0ΦのMCWにより下盛りする時の溶接作業時間、作業費及び溶材費を比較したものです。図から明らかな通り、MCWはソリッドワイヤにくらべ、作業時間において、板厚70mmで約1時間、100mmで2時間も短縮できます。これが作業費の大幅低減を生むため、MCWの単価高による溶材費のアップ分を差し引いても、MCW採用により顕著なコスト低減が計れます。
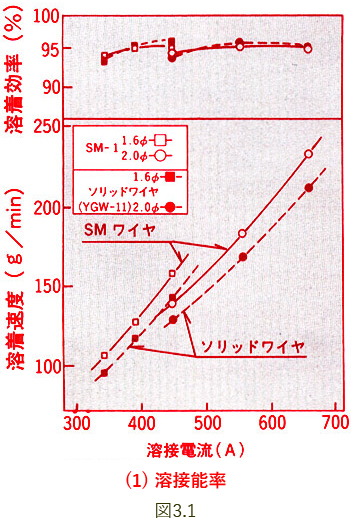
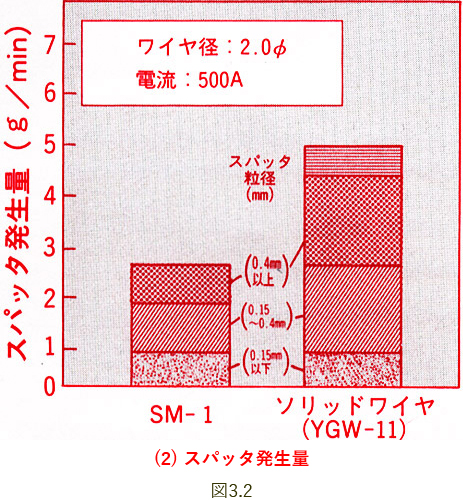
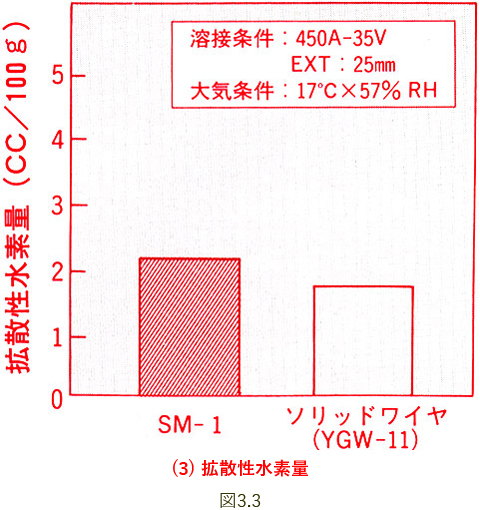
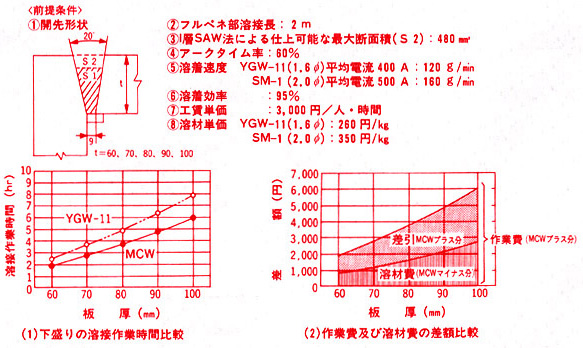
図4
3. 下盛りCO₂溶接こ対するSM-1の適用例
今回、板厚ボックス柱かど継手に対する(SM-1下盛りCO₂溶接+1層SAW)法の実績を、株式会社エモト殿より提供いただいた資料により紹介します。工事は板厚60、70及び80mmにつき実施されていますが、今回はその一例として、80mmの溶接条件を表4に示します。開先は20°の狭開先とし、下盛りには2.0ΦのSM-1が採用されています。太径ワイヤを使用するのは、開先底部においてアークを極力広げ、ここに生じ易い融合不良を防止するためです。また、ガスノズルを2重にするとともに、CO₂の流量を多くすることにより、大電流溶接におけるガスシールド効果を向上させています。電流は500~550Aの高目を採用することにより、60g/min以上の高溶着速度を得ています。表5はSM-1による溶接金属の機械的性質を示したものです。後層SAWによる熱影響にも拘わらず、強度及び衝撃じん性ともに満足な性能が得られています。写真1・写真2・写真3・写真4に溶接状況、ビード外観及び溶接部のマクロ断面を示します。最終層は1層SAW法にて平滑な外観と安定した溶込みが確保されています。
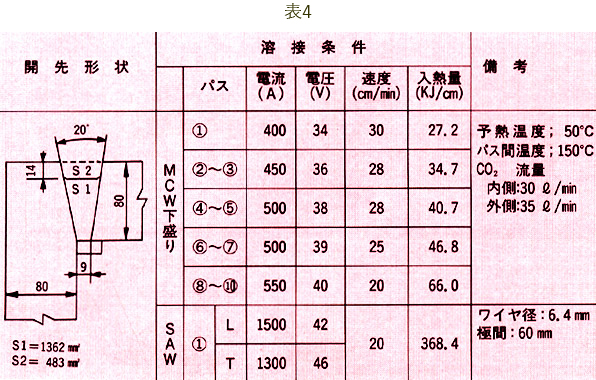
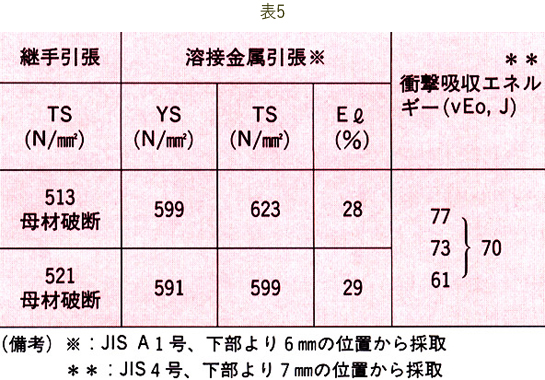
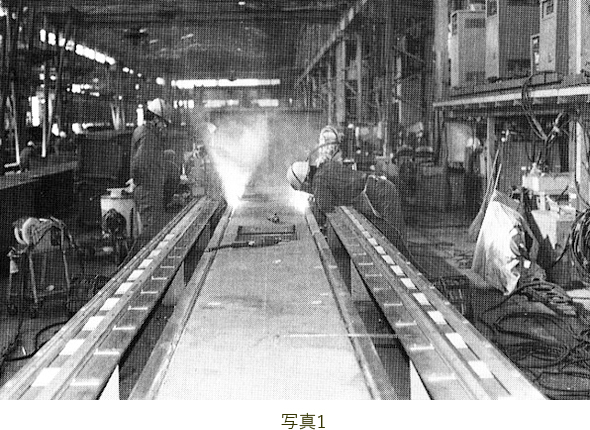
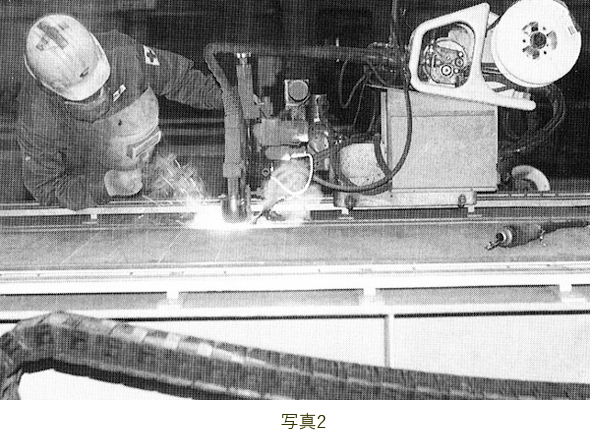
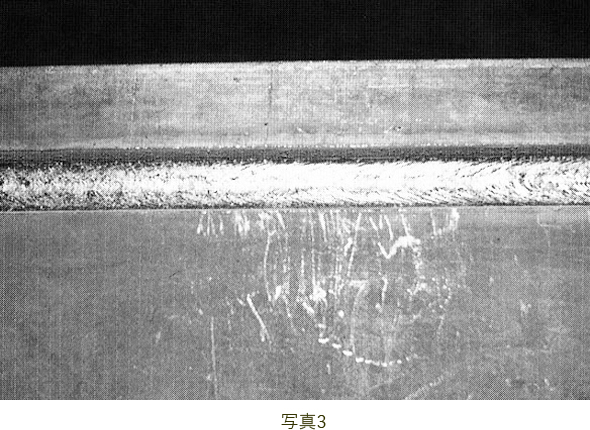
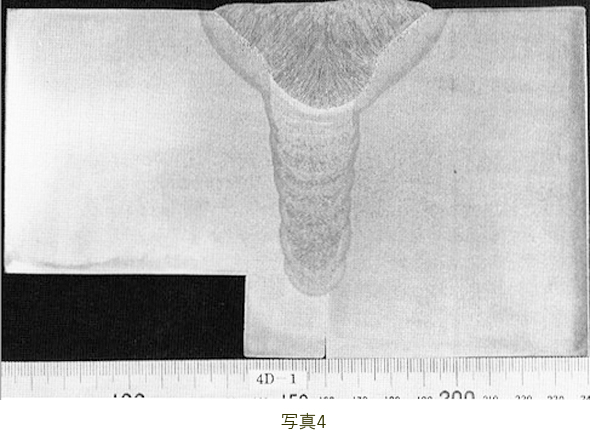
上記ユーザーにおけるSM-1の使用評価は以下の通り極めて満足なものです。
(1)UT合格率が高い。
(2)スパックが少ない。
(3)溶接欠陥がない。
(4)高電流を適用するため、能率が高い。
なお、太径のSM-1を適用することにより、ソリッドワイヤにくらべ、約1.5倍の作業能率が得られています。