技術情報溶接Q&A
F007高速FCuB片面溶接法(NH-HISAW法)について
1. はじめに
造船の大板継ぎに用いられるFCuB片面サブマージアーク溶接は、パネルアッセンブリー工程の流れ作業化に大きく寄与し、すでに20年以上にわたり各造船所で広く適用されている高能率溶接方法です。この間、ラインウェルダーや簡易自走台車の導入により、ロンジのすみ肉溶接の自動化・高能率化は著しく進歩しました。また、海洋の油汚染防止のため、米国ならびにIMO・MEPC(国際海事機関海洋環境保護委員会)のタンカーに対する二重構造(ダブルハル、ダブルボトム)法制化の動きもあり、板継ぎ工程のより高能率化が必要となってきました。
このような背景のもとに、FCuB片面溶接の速度を2倍以上にする事を目標に日立造船㈱有明工場と新日本製鐵㈱、当社の共同研究により、4電極による高速片面溶接法(NH-HISAW法)が開発され、実用化以来すでに1年以上経過いたしました。
以下に本法についてご紹介いたします。
2. 溶接方法の概要
本法は4電極を用い、第1、第2電極で裏ビードを、第3、第4電極で表ビードを形成するもので、たとえば板厚16mmの場合1.5m/minの高速度が得られます。●2-1 裏当て方法
FCuB片面サブマージアーク溶接は図1に示すように、裏当て銅板上に裏フラックスを散布し、エアーホースによりこれを大板の裏面に押し上げ、表側より多電極サブマージアーク溶接を行い、表側と裏側に同時にビードを作る溶接方法です。
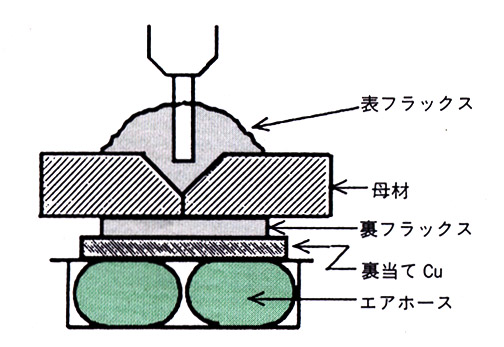
図1
●2-2 裏ビードの形成
本法の基本概念図を図2に示しますが、裏ビードは従来法と同様に第1、第2の先行2本の電極で作ります。
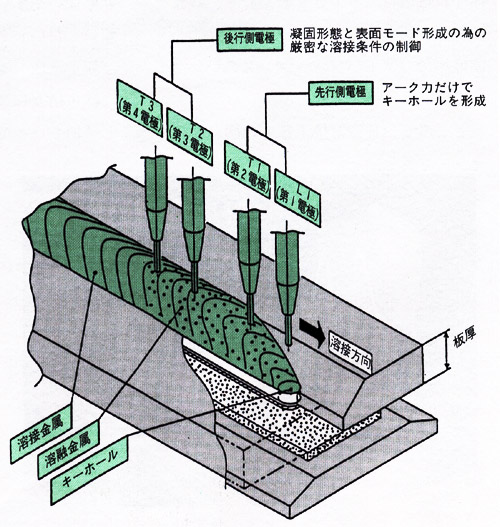
図2
しかし、高速溶接では溶融金属の二次溶融による溶込み効果があまり期待できず、先行電極のアークカのみでキーホールを形成するため、従来法より高い電流が必要となります。
たとえば、開先角度が50°でルートフェースが3mmの場合、速度1.5m/minで良好な裏余盛高さを作るには第1電極と第2電極の電流の合計が約3000A必要となります。写真1に裏ビードの外観を示します。
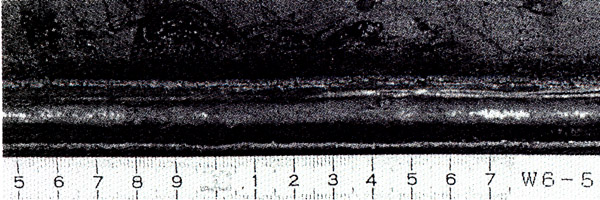
写真1
●2-3 表側の溶接
表ビードは第3、第4の後行2本の電極で作りますが表ビードを作る際に重要なことは、以下の点です。
①アンダーカットを防止すること
②適正な余盛量(溶着金属量)を確保すること
③溶接金属の割れを防ぐため、後行電極の溶込みを十分深くし、先行電極のデンドライトの成長を上向き方向にすること
これらを満足するために、適正な溶接条件(特に電流)と先行電極一後行電極(第2-第3電極)の間隔を適正に選ぶ事が必要で、本法ではこの間隔を200mmに設定しています。
FCuB片面サブマージアーク溶接に使用されるフラックスには、能率を上げるため鉄粉が含まれています。このため、溶着金属量はワイヤとフラックスから供給される金属量で決まります。従って、電流はこの点も加味して決めます。
後行電極の溶込みは、溶液電流と共に先行電極溶接金属の温度や状態により異なります。従って、第2-第3電極間が大きくなったり、あるいは小さくなったりすると、溶込みや表ビードに不具合が発生します。このため、適正な電極間隔を保つことが非常に重要です。写真2に4電極溶接の表ビード外観とマクロを示します。
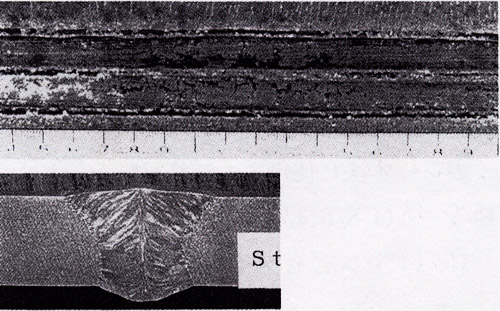
写真2
3. 溶接条件
表1に代表的な標準溶接条件の一例、図3(次頁)に従来法との溶接速度の比較を示しますが、板厚9~16mmの範囲では従来の2倍以上の溶接速度が得られております。表1
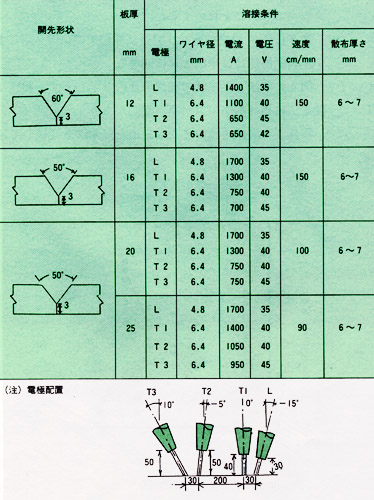
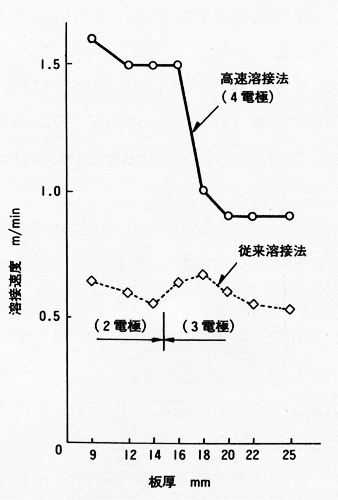
図3
なお、この条件は、第1、第2電極に2000Aの電源容量を用いた場合ですが、18mm以上の厚板側の高速化をさらに進めるには、より大きい電源容量が必要となってきます。なお、本法においては工場における作業効率向上のため電極間隔、電極角度およぴワイヤ等は板厚に関係なく一定にしています。
4. 溶接材料および溶接金属の特性
表2に本法に使用する溶接材料を示します。ワイヤはY-A(4.8/6.4/6.4/6.4mmΦ)、裏フラックスはNSH-1R(レジン含有タイプ)で、従来法と同一の材料です。表フラックスのNSH-50は、本法では厚板の高電流域で表ビードの中央部がやや凸になる傾向があり、フラックスの改良を行いました。表2
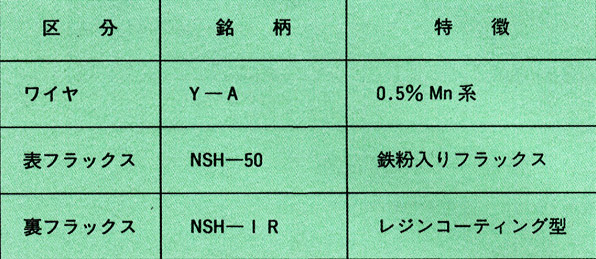
表3にNK規格に準じた引張試験結果の一例を示します。引張性能は従来法とほぼ同等なレベルです。
表3
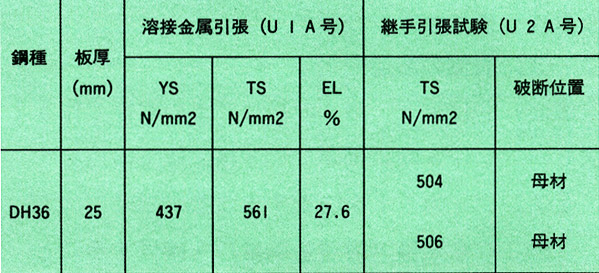
図4に本法と従来法の靱性の比較を示します。靱性は従来法に比べ本法の方が高い傾向があります。
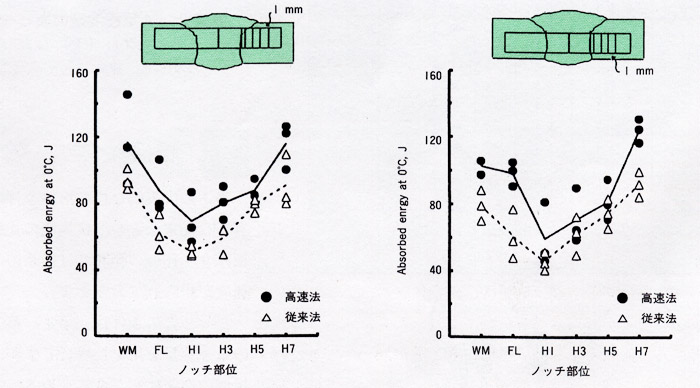
図4
写真3に溶接金属のミクロ組織を従来法と比較して示します。溶接金属は初析フェライト(F)とべイナイト(Bu)の混合組織を呈しますが、本法の方が入熱が低く冷却速度が速いため初析フェライト量が少なく、ベイナイト組織も細粒化しています。
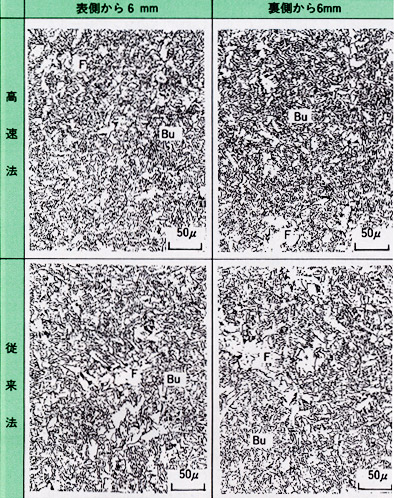
写真3
5. 実用特性 - 溶接変形への影響 -
従来法と比べ本法の溶接条件は入熱が低く、溶接熱による応力の低減が期待されます。実験室での検討時や工場適用後、特に薄板側の高速溶接において、鋼板の変形(角変形)が少ないことが観察されました。これらから、終端割れの主因である回転変形も減少していることが期待されます。図5に板厚と終端部の回転変形量の関係を示します。従来法の変形量はほぼ1mmであり、板厚による差は余りありません。一方、本法の場合、20mm以上の板厚では変形量は従来法と同等ですが、板厚が16mm以下では従来法の変形に比べ半減しています。本法の板厚16mm以下の溶接速度は1.5m/minであり、高速化が変形量低減に有効と考えられます。
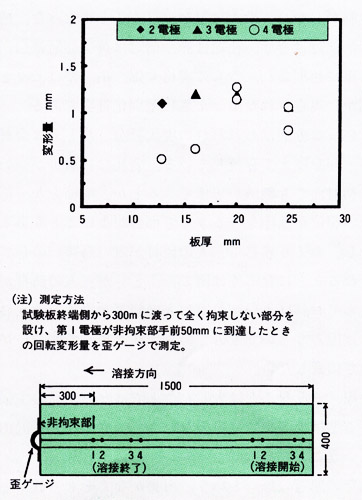
図5
6. おわりに
以上、造船用板継ぎ溶接において溶接速度を従来の溶接法に比ベ2倍以上と、飛躍的に高める高速片面溶接法について紹介しました。今後も、技術の進歩と品質に対する要求に応えることを目標として、需要家各位との緊密な連係のもとに新規の溶接方法や、溶接材料の開発に努めたいと考えています。