技術情報溶接Q&A
F012薄板のガスシールドアーク溶接
1. はじめに
アーク溶接の分野での半自動化、自動化、ロボット化の急速な進展に伴い、ガスシールドアーク溶接が溶接分野で主役の座を占めてからすでに10年になろうとしており、図1の国内向け溶接材料出荷高推移に見られるように、平成に入ってからは常に60%以上の高率を保っています。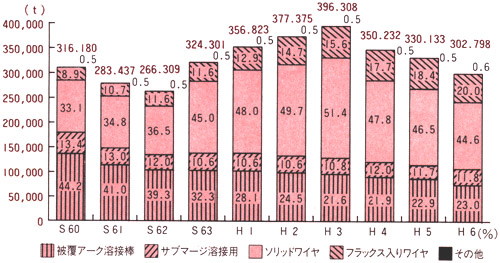
図1
さらに、薄板の代表的使用者である自動車・車両の部門では、図2の業種別溶接材料の使用比率を調査した結果で明らかなように、ほとんどがソリッドワイヤ、フラックス入りワイヤを使用したガスシールドアーク溶接であることがわかります。
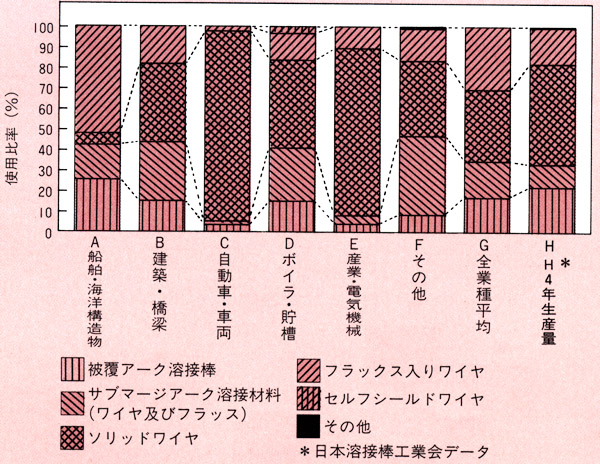
図2
今回は、薄板のガスシールドアーク溶接について各種問題解決の手法や、専用のワイヤ開発状況等を紹介いたします。
2. 薄板の溶接に求められる特性
表1は日本溶接協会の調査(1991年)による「溶接材料、溶接電源の業種別開発要望」のガスシールドアーク溶接材料に関する部分の抜粋です。ソリッドワイヤ、フラックス入りワイヤともにスパッタの少ないもの、耐ピット・耐ブローホール性の良いものが上位にランクされています。また、ソリッドワイヤではビード外観の改善、フラックス入りワイヤではヒューム低減が強い要望となっています。これらの要望に対し、当社は低スパッタワイヤの開発、亜鉛めっき鋼板用ワイヤの開発及びその溶接技術開発等を実施してきました。さらに最近、自動車や電気など薄板の溶接でも、高速溶接が求められ溶接時の溶落ちによる穴あきや、シールドの乱れによる気孔発生の問題解決がユーザーの方々から強く要望されています。表1
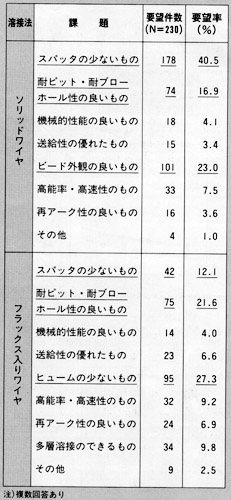
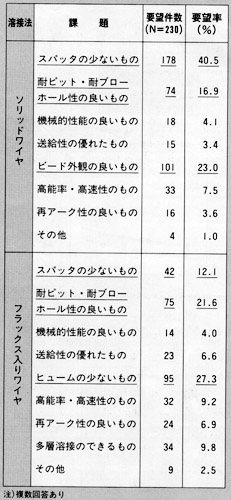
3. 低スパッタ溶接
ガスシールドアーク溶接における低スパッタ化は、スパッタ付着量の減少による清掃時間の短縮はもちろんのこと、溶接者の疲労軽減、溶接部の信頼性確保にもつながり、大きな効果をもたらします。スパッタの低減方法としては、
①使用ワイヤの選択、
②シールドガス組成の選択、
③溶接電源の選択が最も有効です。
最近の溶接性改善に対する溶接電源の開発は目覚しいものがあり、特にトランジスタ・インバータ制御による高速で精密な電流波形制御が可能になったことから、溶接現象そのものを制御する方法が採用され、短絡移行時の溶滴の制御によりスパッタの発生量を飛躍的に抑制できるようになりました。インバータ電源における波形制御によるスパッタ低減の概念例を図3に示します。
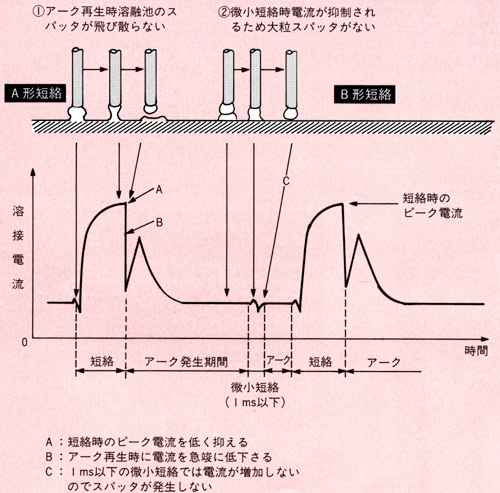
図3
YM-24Sは高性能インバータ制御のパルスマグ溶接機に合わせた専用ワイヤとして開発されたものです。このワイヤはアーク現象に基づき、合金成分や添加成分を調整することにより、電源の波形制御に応じて溶滴を冶金的に細粒化し移行させるように設計されたものです。図4に示すように従来法に比べ、スパッタ量は1/5以下になっています。
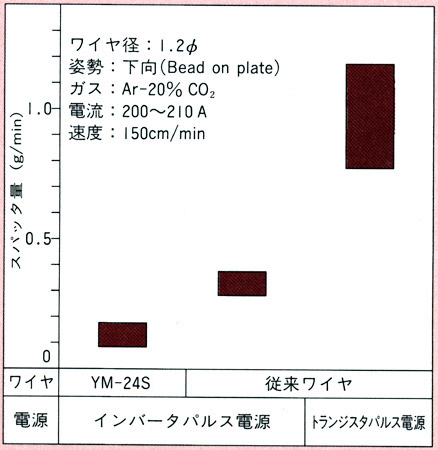
図4
また、図5はソリッドワイヤにおけるノズルに付着するスパッタ量に及ぼすシールドガス組成の影響を調べたもので、CO₂ 50~100%に比較しAr+10~20%CO₂では格段にスパッタの低減が図れます。
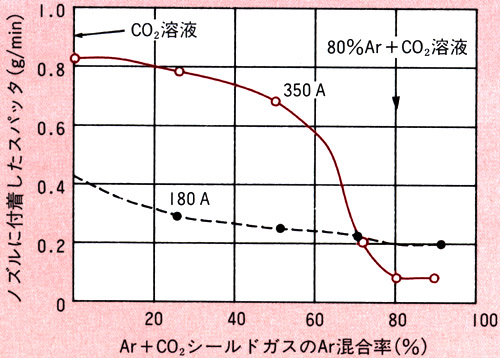
図5
4. 亜銘めっき鋼板の溶接
薄板の代表的使用部門である自動車では防錆基準の強化に伴って表面処理鋼板が多く使われています。中でも、亜鉛めっき鋼板は、鋼の優れた強度・加工特性に比較的安価で優れた耐食性をもたせることのできる優れた鋼板で広く採用されています。
しかし、亜鉛めっき鋼板の溶接では、発生する亜鉛蒸気によりアークが不安定になり、スパッタの発生やピット、ブローホール等の気孔欠陥の発生が問題となり、溶接電源特性や専用ワイヤの開発等の検討がなされました。
YM-22Zは合金化溶融亜鉛めっき鋼板溶接専用ソリッドワイヤとして開発されたもので、溶接時の亜鉛の蒸気発生を抑制し、アークの安定性を確保するとともに、溶融池の粘性を適正化し気泡の浮上が容易になるように設計されています。パルス電源との組合わせにより大幅に気孔やスパッタの発生が低減できました。
図6に専用ワイヤYM-22Zと従来ワイヤの溶接姿勢と気孔発生の関係を示します。
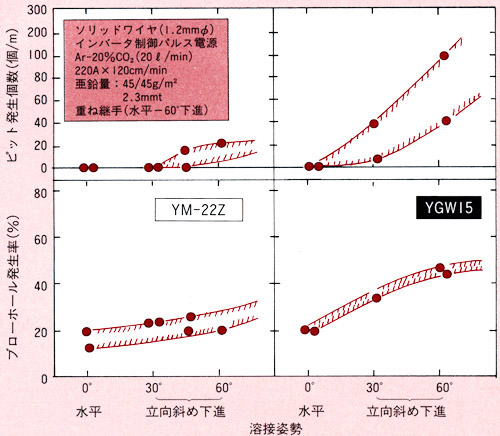
図6
さらに、フラックス入りワイヤの特長を生かしながら、低スラグ化を実現し、YM-22Zと同様の手法により、亜鉛めっき鋼板での耐気孔性を良好にしたメタル系フラックス入りワイヤSM-2ZAも開発されております。
自動車部品等の薄板の合金化溶融亜鉛めっき鋼板の溶接では、高速溶接(100cm/min以上)、低スパッタ、ビード形状確保の点から、シールドガスとしてAr-CO₂を使用したパルスマグ溶接が行われています。図7にパルスピーク電流及び周波数を変化した電源による耐気孔性の調査結果を示します。パルス電源の種類、パルス条件も気孔の発生に影響があり選定が重要です。
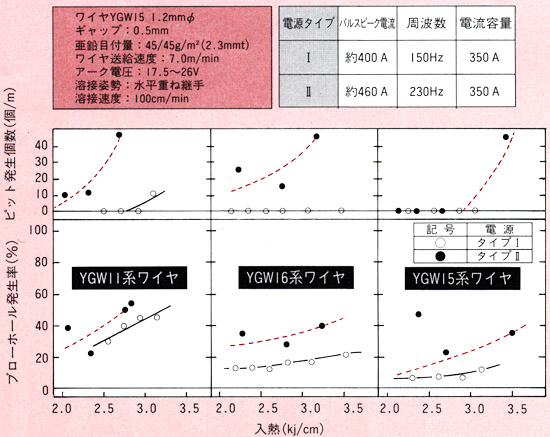
図7
5. 耐溶落ち・耐シールド不良
薄板の溶接では、溶接中の溶落ち防止のため低電流・低速度溶接が行われてきました。しかし、能率面の向上要望から薄板のガスシールドアーク溶接においても高速化が望まれています。高速溶接では溶落ちによる穴あきとともに、溶接雰囲気のシールドが乱れ大気が混入しブローホールが発生し易くなり、これらの防止が課題でありました。
YM-30はこのような課題解決のため新規に開発されたワイヤです。このワイヤは合金成分や添加成分を調整することにより、ビード形状が平らでビード幅が広く、溶込みが浅くなるように設計されています。そのためギャップのあるところでも架橋性が優れています。さらに、ワイヤ中にシールド不良に対応する元素を添加し、大気混入による気孔欠陥を軽減できるように設計されております。ビード外観および耐ギャップ性の状況を写真1に示します。
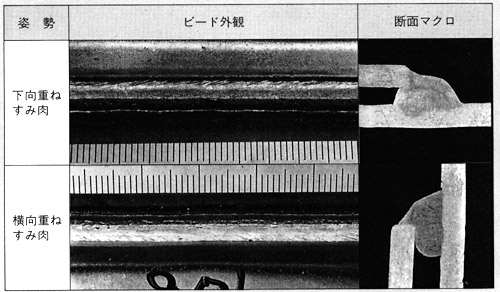
写真1
また、フラックス入りワイヤは、溶込みが浅く、ビードに広がりを持つ特長があり、薄板での耐溶落ち性改善に有効です。先に紹介した、亜鉛めっき鋼板用SM-2ZAはこの面でも優れた性能を示し、薄板の溶接に適しています。重ねすみ肉溶接での断面の溶込み状況をソリッドワイヤと比較し図8に示します。
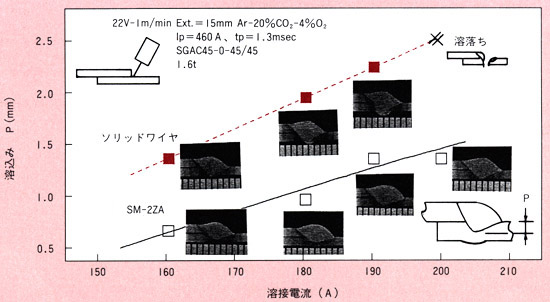
図8
YM-28Zは、本来、溶融亜鉛めっき鋼板用に開発されたワイヤで、比較的厚日付け(Z27:270g/m²程度)の鋼板のCO₂溶接でビード外観に優れ、ブローホール、スパッタ発生の少ない特性を有していますが、普通鋼板の薄板の溶接でも耐溶落ち性、耐シールド性に優れ、スパッタの発生が少なく、良好なビード外観が得られることが確認されています。ビード外観及び耐ギャップ性の状況を写真2に示します。
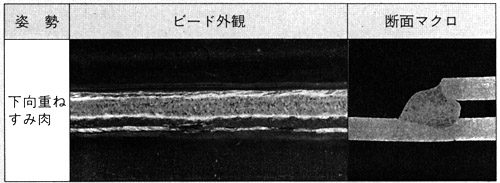
写真2
6. おわりに
薄板用ガスシールドアーク溶接について各種特性を述べてきましたが、実際の使用にあたっては、使用部材や使用条件に応じたワイヤを選定することが重要です。当社にはそれぞれの特性をより効果的に発揮するワイヤが開発されています。当社薄板用ソリッドワイヤの特性を表2に示します。ワイヤを選定の際の参考にして下さい。
表2
銘柄 | 対応JIS (Z3312) |
耐ギャップ性 | ビード外観 | 低スパッタ | 耐気孔性 | |
シールド不良 | 亜鉛メッキ | |||||
YM-28 | YGW12 | 〇 | 〇 | 〇 | 〇 | - |
YM-28S | YGW15 | △ | 〇 | 〇 | 〇 | - |
YM-24S | YGW17 | 〇 | △ | ◎ | △ | - |
YM-2S | YGW16 | ◎ | 〇 | 〇 | △ | - |
YM-22Z | YGW17 | △ | △ | ◎ | ◎ | ◎ |
YM-28Z | YGW14 | ◎ | ◎ | ◎ | 〇 | 〇 |
YM-30 | YGW17 | ◎ | ◎ | ◎ | ◎ | - |
◎:非常に優れる、〇:良好、△:運用可能、✕:劣る
これまで述べてきましたように、ガスシールドアーク溶接の分野では、ワイヤの特性、電源特性、溶接施工条件等を適正に組合わせることにより大きな効果が発揮されます。今後も総合技術として、各分野が孤立せず協力して進展させて行くことが必要と考えます。当社も技術革新に向けて、一層努力してまいります。
<引用文献>
1)日本溶接棒工業会:溶接展望No.60
2)日溶協 溶接棒部会:溶接の研究No.31
3)原田、安田:「炭酸ガス・マグ溶接におけるスパッタ低減の方法」溶接技術41-2
4)本誌No.102
5)本誌No.104