技術情報溶接Q&A
F064W-PLASMAによる高速化の実現
1. はじめに
プラズマ溶接は図1に示すように、水冷チップを介してプラズマ気流中をタングステン電極から母材にアークを移行する非消耗式溶接法です。プラズマアークは、水冷チップで収束されるため、高熱エネルギー密度アーク溶接となり、突合せ溶接ではTIG法と比して、約1.5~4倍の溶接速度が得られ、ひずみの少ない高品質溶接ができます。
また、溶接はノンスパッタのクリーンアークで行うので、美麗なビード外観を呈します。
このような溶接結果が得られることで、プラズマ溶接はTIG法やCO₂溶接法におけるビード外観・品質の問題解決として、幅広い分野に適用・拡大されてきました。
一方、レーザー法と比べるとプラズマ溶接は設備コストが低いものの、突合せ溶接の速度が2~4倍ほど劣っていました。そこで製造現場からは、プラズマ溶接でもレーザー溶接に近い高速溶接が実現しないか、開発が期待されていました。
今回、従来のプラズマ法より2~3倍の高速溶接を可能にした2電極プラズマ溶接法を開発しましたので紹介いたします。
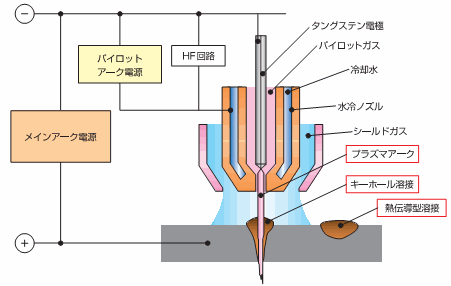
図1 プラズマ溶接原理
2. 従来プラズマ法での高速溶接時の課題
図2の模式図に示すように、従来のプラズマ溶接では、適正溶接速度を超えるとビード両端にアンダーカットが発生します。このアンダーカットの発生が、高速溶接化の課題でした。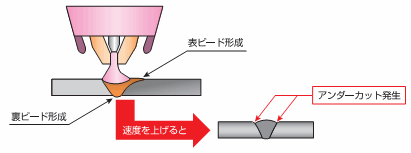
図2 従来プラズマ溶接のビード形成
●2電極プラズマ溶接法
1)原理と特長図3は2電極プラズマ溶接法(以下2電極溶接)の原理を示すもので、先行アークはシャープなアークで裏ビードを形成し、後行アークはソフトなアークによって先行アークで発生したビード両端のアンダーカットを再溶融し、平滑な表ビードに成形します。
このように、ビード形成をそれぞれ役割分担することで、最適条件で溶接できます。また、後行アークで先行ビード上を再溶融することで、高速溶接でも内部欠陥が発生しづらい溶接法となります。
図4は熱伝導型アークで薄板溶接を行った時の熱源形状と溶融プール形状を示しております。2つのアークは至近で発生していることから、その熱源形状は溶接線上に細長い形状となり、その結果、溶融プールも連続化した細長いプールとなり、高速溶接に最適な熱源形状となります。
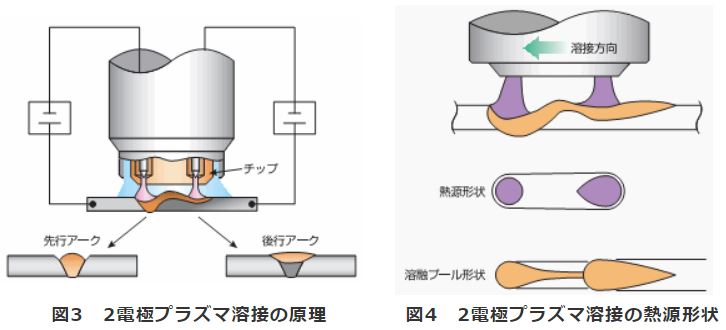
2)設備の構成
2電極溶接の主設備は図5に示す構成となります。プラズマ溶接機と2電極プラズマトーチを写真1に示します。トーチはシンプルなストレート形状で取り扱いやすい形状となっています。トーチ先端部のチップには、2個のアーク噴出孔が設けられています。
2電極溶接の主設備は図5に示す構成となります。プラズマ溶接機と2電極プラズマトーチを写真1に示します。トーチはシンプルなストレート形状で取り扱いやすい形状となっています。トーチ先端部のチップには、2個のアーク噴出孔が設けられています。
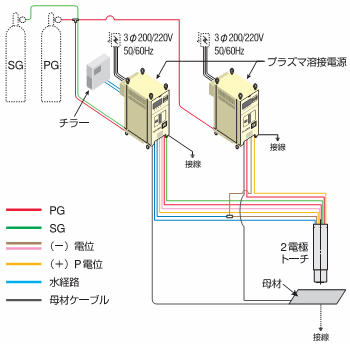
図5 W-PLASMAの構成
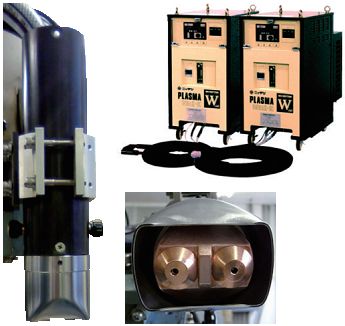
写真1 プラズマ溶接機と2電極プラズマトーチの外観
3.従来技術との比較
1)溶接速度
図6に軟鋼材での溶接速度のグラフを示します。2電極溶接は従来法と比べ2~3倍の高速化が図れます。ステンレス鋼(オーステナイト・フェライト系)でも軟鋼と同様な結果が得られ、従来法より2~3倍の高速化を図ることができます。
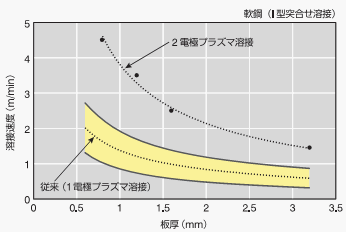
2)ビード横断面のマクロ・ミクロ組織
写真2に軟鋼材、SUS304材およびSUS409L材の横断面マクロ・ミクロ組織を示します。
軟鋼材では板厚1.6mmの熱伝導型突合せ溶接金属の凝固形態を確認しました。
最終凝固部を見ると、従来法が上向き凝固+等軸晶に対し、2電極法は突合せ凝固組織(高速溶接でみられる組織)を呈しています。
図6に軟鋼材での溶接速度のグラフを示します。2電極溶接は従来法と比べ2~3倍の高速化が図れます。ステンレス鋼(オーステナイト・フェライト系)でも軟鋼と同様な結果が得られ、従来法より2~3倍の高速化を図ることができます。
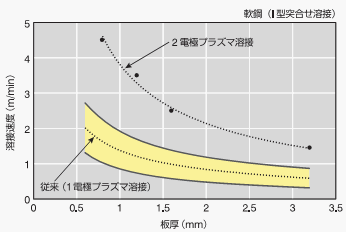
写真2に軟鋼材、SUS304材およびSUS409L材の横断面マクロ・ミクロ組織を示します。
軟鋼材では板厚1.6mmの熱伝導型突合せ溶接金属の凝固形態を確認しました。
最終凝固部を見ると、従来法が上向き凝固+等軸晶に対し、2電極法は突合せ凝固組織(高速溶接でみられる組織)を呈しています。
供試材料 | 溶接法 | ビード断面 | 速度 (m/min) |
||
材質 | 板圧 | マクロ組織 | ミクロ組織 | ||
軟 鋼 | 1.6 | 2電極 | ![]() |
- | 2.5 |
従来 (1電極) |
![]() |
- | 1.0 | ||
SUS304 | 5.0 | 2電極 | ![]() |
![]() |
0.8 |
従来 (1電極) |
![]() |
![]() |
0.4 | ||
SUS409L | 1.5 | 2電極 | ![]() |
![]() |
2.1 |
従来 (1電極) |
![]() |
![]() |
0.6 |
写真2 従来とのマクロ断面比較
SUS304は板厚5mmの突合せキーホール溶接金属のマクロ断面で、2電極溶接は2プールで凝固し、結晶粒も小さいことが確認されました。
写真3は両者ナゲット形状の大きさを重ねて比較した写真です。従来法より約30%減の断面積となっており、その分、低入熱・低歪みの溶接となります。
SUS409Lは板厚1.5mmの熱伝導型突合せ溶接金属で、マクロ・ミクロ写真で明らかなように、2電極溶接の結晶粒がより微細化されています。その分、プレス加工などの後加工で、優位に働くものと思われます。
写真4にテーラードブランク方式で生産される差厚溶接への2電極溶接事例として、軟鋼材の0.8tと1.6tのビード外観とマクロ断面を示しますが、健全な溶接結果が得られています。
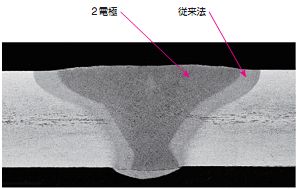
写真3 溶け込み形状比較例(SUS304、5t)
表ビード/裏ビード | マクロ断面 | 速度 (m/min) |
![]() |
![]() |
3.4 |
![]() |
3)機械的性質
(1)エリクセン試験
エリクセン試験でSUS409Lにおける溶接金属部の張り出し成形性を確認した結果を図7に示します。2電極溶接、1電極溶接共に、ほぼ同等のエリクセン値を示しており、溶接後のプレス成形性に大差がないことが判りました。
(2)硬さ試験
図8に硬さ試験結果を示します。2電極溶接のHAZ部およびWM部の硬さは1電極溶接よりやや軟らかい傾向で、これは溶接後のプレス成形性の向上に寄与できるものと考えられます。
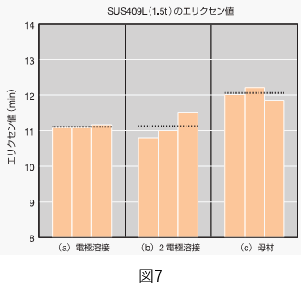
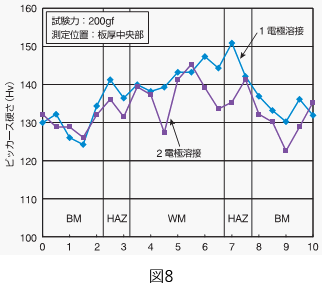
4. おわりに
以上述べましたように、新規開発した2電極溶接は従来法の2~3倍の高速溶接化が図られ、かつ、高品質溶接と美麗なビード外観が得られました。
今後は高速溶接化が要望される自動車の車体部品、ステンレス造管などの突合せ溶接分野で、コスト低減・品質向上などの課題解決に貢献できる技術と考えています。
当社では今後もユーザーの皆様からのご要望にお応えするため、商品の改良・開発に努めますので、ご愛顧のほど、よろしくお願いいたします。
今後は高速溶接化が要望される自動車の車体部品、ステンレス造管などの突合せ溶接分野で、コスト低減・品質向上などの課題解決に貢献できる技術と考えています。
当社では今後もユーザーの皆様からのご要望にお応えするため、商品の改良・開発に努めますので、ご愛顧のほど、よろしくお願いいたします。