技術情報溶接Q&A
F042シームレスフラックス入りワイヤの基本特性(SF/SMワイヤ-進化への基盤)
はじめに
ガスシールドアーク溶接用のフラックス入りワイヤは、溶接の高能率性ばかりでなく、溶接しやすく良好なビード形状、外観が得られるワイヤとして、この四半世紀で大きく発展しました。当社のシームレスフラックス入りワイヤは、1981(昭和56)年の販売開始以来、今日までSF/SMワイヤとして、ユーザーの皆様にはたいへんご愛顧いただきながら成長してきました。
今回はSF/SMワイヤの優れた品質基盤となっているシームレスフラックス入りワイヤの基本特性について、以下にご紹介します。
シームレスフラックス入りワイヤの断面形状
写真1に当社の全姿勢溶接用シームレスフラックス入りワイヤSF-1のワイヤ断面形状を示しました。フラックス入りワイヤとは外皮金属の内部に所定の溶接性能が得られるよう調整されたフラックスが充填されているワイヤで、外皮部に隙間(合わせ目有り、シーム有り:以後、シーム有りワイヤと呼びます)があるものと、隙間のないもの(合わせ目無し、シーム無し:以後、シームレスフラックス入りワイヤと呼びます)とに分けられます。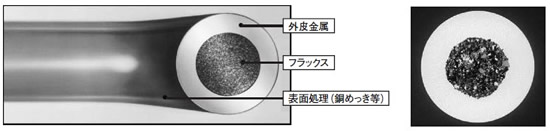
写真1 全姿勢溶接用シームレスフラックス入りワイヤSF-1のワイヤ断面形状
シームレスフラックス入りワイヤの製造工程
図1にシームレスフラックス入りワイヤの製造工程を示しました。連続的に供給される外皮帯鋼をU型に成形し、フラックスを充填後、造管溶接を行い、シームレスのフラックス充填管とします。内部のフラックスが完全密閉されたことにより、フラックスが持ち込んだ水分を除去するための高温度脱水素処理や銅めっきなどの湿式表面処理が可能になります。
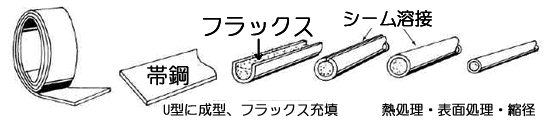
図1 シームレスフラックス入りワイヤの製造工程
シームレスフラックス入りワイヤの基本特性
表1にシームレスフラックス入りワイヤの基本特性をまとめて示しました。外皮部に隙間がないことに加えて、製造工程に組み込まれた高温脱水素処理や湿式表面処理による効果が相まって、シームレスフラックス入りワイヤの基本特性となっています。表1 シームレスフラックス入りワイヤの基本特性
外皮部に隙間がない | ワイヤ断面形状が均一 | 耐吸湿性に優れる ターゲット性に優れる |
高温脱水素処理が可能 | 極低水素 | 耐気孔性、耐低温割れ性に優れる |
湿式表面処理が可能 | 銅めっき | 通電性およびチップの耐摩耗性が 良好でアークが安定する 耐錆性に優れる |
銅めっきなし(特殊処理) | 同上 |
1.低水素
シームレスフラックス入りワイヤの溶接特性の第1は極めて低い水素量にあります。溶接材料が低水素であることは、厚板の多層盛溶接や高強度鋼溶接で問題になる低温割れの防止、また、プライマ塗装鋼板の高速すみ肉溶接で特に問題となる気孔(ピットやブローホールなど)発生防止の観点からも、基本用件と考えます。
シームレスフラックス入りワイヤでは、製造工程中の高温脱水素処理により、ワイヤ自体(フラックス)がもつ全水素量を極めて少なくしていること、外皮部に隙間がないので、溶接現場のさまざまな使用環境や長期保管中の内部フラックスへの吸湿は全く起こりません。
海浜の溶接現場や湿度100%で露点を結ぶような梅雨時の溶接など、ワイヤの吸湿の影響は極めて大きいものとなります。
図2に、フラックス入りワイヤの全水素量を変化させた試作ワイヤによる拡散性水素試験結果を示しました。
全姿勢溶接用シームレスフラックス入りワイヤSF-1のワイヤ全水素量は15ppm以下、拡散性水素量は2~3ml/100gであり、極めて低水素域になっています。
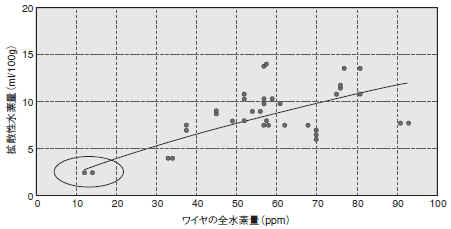
図2 フラックス入りワイヤの全水素量と拡散性水素量の関係
(JIS Z 3118 鋼溶接部の水素量測定方法)
図3に強制吸湿条件下で行ったフラックス入りワイヤの吸湿試験結果を示しました。大気からの吸湿によるワイヤ水分量の増加は、確実に拡散性水素量を増加させることになります。
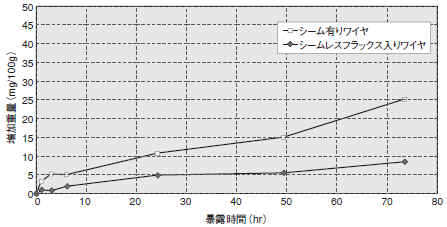
図3 フラックス入りワイヤの吸湿試験結果
(温度30℃-湿度80%雰囲気)
図4に耐低温割れ性に及ぼす拡散性水素量の影響(板厚32mm-U型溶接割れ試験結果)を示しました。健全な溶接部を得るためには、ワイヤの低水素化がいかに重要であるかがわかる試験結果となっています。
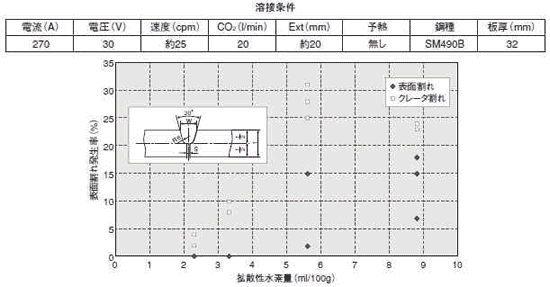
図4 耐割れ性に及ぼす拡散性水素量の影響
(JIS Z 3157 U型溶接割れ試験)
2.ワイヤのターゲット性
シームレスフラックス入りワイヤの溶接特性の第2は良好なターゲット性(直進性)です。造船現場の横向板継ぎ溶接、ロンジ材の高速水平すみ肉溶接、すみ肉簡易走行台車溶接、橋梁のUリブ溶接、ロボット溶接などの自動溶接または半自動溶接において、溶接中のワイヤ先端部の狙い位置の正確さがビード形状から溶接欠陥の発生有無までも左右します。特に高速水平すみ肉溶接やロボット溶接ではワイヤのターゲット性が非常に重要で基本品質となっています。シームレスフラックス入りワイヤのターゲット性は、ワイヤ断面の外皮部に隙間がなく、断面が対称形であり捩れにくいことに加えて、後記耐チップ摩耗性向上も大いに寄与しています。
3.チップの耐摩耗性
シームレスフラックス入りワイヤは、ワイヤ断面の外皮部に隙間がないことから、さまざまな湿式処理(表面処理、銅めっきなど)が施せることから、シーム有りワイヤにはない特長を持たせることが可能です。
その一例として、ワイヤ表面に銅めっきを施した場合、銅めっきは、ワイヤと溶接チップ間の通電性を高め、チップの耐摩耗性を向上させることにより、アーク安定性を保持する効果を出しています。
また、銅めっきなしタイプのシームレスフラックス入りワイヤである(SF-1エコ)の場合は、銅めっきに代わる特殊なワイヤ表面処理の開発により、銅めっきありワイヤの良好な耐チップ摩耗性の維持とともに良好なアーク安定性が得られています。
図6にシームレスフラックス入りワイヤとシーム有りワイヤの溶接チップ摩耗量の比較結果を示しました。
溶接を合計で100分間(10分×10回)行い、チップの穴径がどれくらい広がっているかを計測して評価したものです。シームレスフラックス入りワイヤのチップ摩耗性が良好なことがわかると思います。
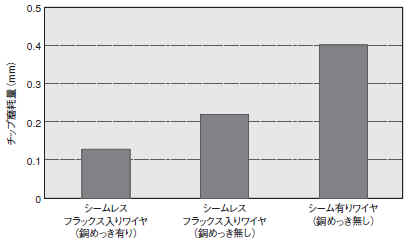
図6 チップ摩耗量
(チップ先端部の穴径の最大幅)
4.アークの安定性
シームレスフラックス入りワイヤは、チップの耐摩耗性が良好なことから、安定したアーク状態が長期間得られます。図7は摩耗したチップの断面模式図を示しています。チップ摩耗は主に先端部分に集中しており、新品のチップに比較して、摩耗したチップを使用した場合、ワイヤへの給電点が上方に移り、ワイヤ突き出し長さを長くして溶接した場合と同じような状態となります。
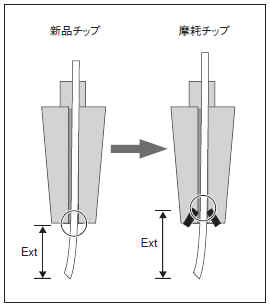
図7 チップ摩耗の概略図
図8は、ワイヤの送給量を変えないで(電流つまみを動かさないまま)、ワイヤの突き出し長さのみを変化させた場合の溶接電流値の変化を示したものです。ワイヤの突き出し長さが長くなった場合、溶接電流が低下していきます。この時のアーク状態は明らかに異常で、特に立向溶接においてアーク長が変動したり、アークのばたつきやスパッタが多く発生しました。
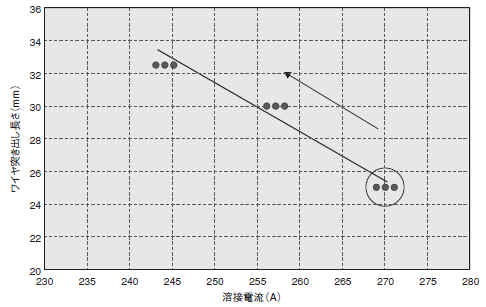
図8 溶接電流とEXTの関係
(同一ワイヤ送給量)
おわりに
フラックス入りワイヤに対し、一段の品質向上、品種拡大、適用範囲拡大の要求、またそれぞれに異なる溶接現場ニーズからの要求など、フラックス入りワイヤへの期待はますます高まっています。シームレスフラックス入りワイヤの基本特性として、特に低水素、ターゲット性、耐チップ摩耗性およびアーク安定性を取り上げました。これらの溶接特性を基盤として、シームレスフラックス入りワイヤは今後ともさらに進化していきますので、引き続いてのご愛顧をよろしくお願いいたします。