技術情報溶接Q&A
F053シームレスフラックス入ワイヤの進歩
1. はじめに
当社のシームレスフラックス入りワイヤは、1981(昭和56)年の販売開始以来、今日までSF・SMワイヤとしてユーザーの皆様には大変ご愛顧いただきながら成長してまいりました。本稿では、その優れた品質基盤となっているシームレスフラックス入りワイヤの基本特性と、より安心してご使用いただけるよう高品質化への取り組みをご紹介いたします。2. シームレスフラックス入りワイヤの特長
図1に当社の全姿勢溶接用シームレスフラックス入りワイヤSF-1の断面形状を示します。ワイヤ製造時に金属外皮の合わせ目を溶接し、内部のフラックスを完全密封することによって、表1に示すような優れた基本特性が得られます。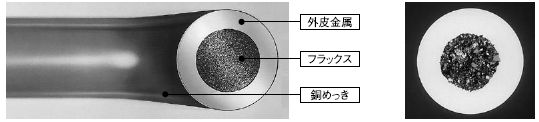
図1 全姿勢溶接用シームレスフラックス入りワイヤSF-1の断面形状
表1 シームレスフラックス入りワイヤの基本特性
シームレス構造の利点 | ワイヤの特長 | 溶接品質の優位点 |
外皮に隙間が無い | 均一なワイヤ断面形状 | ・耐吸湿性に優れる ・ターゲット性に優れる |
高温脱水素処理が可能 | ワイヤ中の水素量が低い | ・耐気孔性に優れる ・拡散性水素量が低い(低温割れ防止に有利) |
湿式表面処理が可能 | 銅めっき | ・ワイヤ送給性に優れる ・チップの耐摩耗性に優れる ・耐錆性に優れる |
3. シームレスフラックス入りワイヤの基本特性
造船、橋梁製作における高速水平すみ肉溶接や、建築、海洋構造物等の多層溶接など、あらゆる溶接部材の製作現場において、溶接中のワイヤ送給性およびターゲット性(ワイヤ先端部狙い位置の正確さ)は、ビード形状や溶接欠陥の有無といった溶接部の品質に直結します。
具体的なシームレスフラックス入りワイヤの基本特性を以下に紹介します。
(1)ワイヤ送給性・耐チップ摩耗性の追求
当社では、安定したワイヤ送給性と耐チップ摩耗性を両立すべく、ワイヤ表面処理技術の開発を行っています。最新技術が適用されたSF-1では、図2~3に示すように、コンジットライナーがロンジ材を跨いでさらに手元でS字屈曲するような非常に厳しい条件でも、安定したワイヤ送給を確保できます。
具体的なシームレスフラックス入りワイヤの基本特性を以下に紹介します。
(1)ワイヤ送給性・耐チップ摩耗性の追求
当社では、安定したワイヤ送給性と耐チップ摩耗性を両立すべく、ワイヤ表面処理技術の開発を行っています。最新技術が適用されたSF-1では、図2~3に示すように、コンジットライナーがロンジ材を跨いでさらに手元でS字屈曲するような非常に厳しい条件でも、安定したワイヤ送給を確保できます。
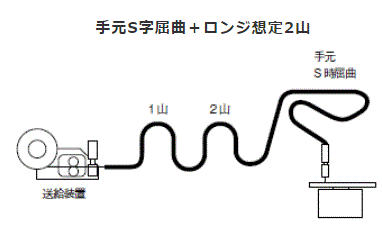
また、耐チップ摩耗性についても、写真1に示すように100分間溶接後のチップ摩耗量は、市販FCWの約3分の1程度と非常に少ない(チップ寿命が長い)ため、チップ交換の頻度が少なく、長時間の溶接でもチップ摩耗によりアーク状態が不安定化する心配が軽減します。
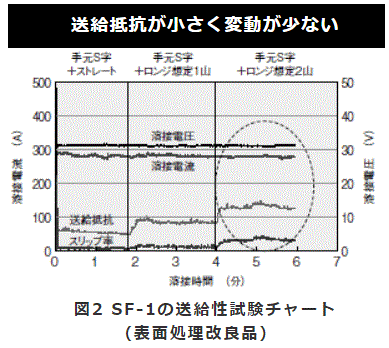
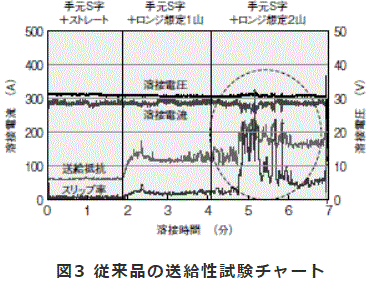
試験条件 | SF-1(シームレス) | 市販のFCW |
連続溶接10分×10回 (累計100分) ワイヤ径:1.2mm 溶接電流:270A チップの摩耗が少ない |
![]() |
![]() |
チップ先端の摩耗量※ | 0.13mm | 0.40mm |
※チップ先端の摩耗量=(溶接後のチップ穴外接円の直径)-(溶接前のチップ穴直径)
写真1 100分間溶接後のチップ摩耗状態
(2)ターゲット性の追求
図4にSF-1によるターゲット性試験の結果を示します。固定したトーチからワイヤを送給し、突き出し長(Ext.)を150mmと極端に長くした位置でワイヤ先端の狙いズレ量を測定しても、狙い位置が極めて安定していることが分かります。これは、シームレスフラックス入りワイヤの断面形状が対象形で捻り剛性が高いため、ワイヤ送給における直進安定性(ターゲット性)が優れていることによります。
試験条件 | SF-1(シームレス) | 市販のFCW |
ワイヤ径:1.2mm (ペイルパック品) ストレートトーチ Ext.:150mm |
ワイヤ狙い位置が極めて安定 ![]() |
![]() |
図4 ワイヤのターゲット性試験
4. シームレスワイヤの新たな挑戦
シームレスフラックス入りワイヤ最大の利点は、ワイヤ自体の水素量を極めて低くできる点にあります。これは、(1)ワイヤ製造時の高温脱水素処理によりフラックスや外皮に付着した水分(水素源)を低減できることと、(2)ワイヤ製造後においても、外皮部に隙間がないシームレス構造であるため、大気中からワイヤ内部への吸湿が全く起こらないことにより達成できるものです。当社では、この低水素をさらに進歩させるべく、技術開発を進めています。(1)低水素化
図5にワイヤの全水素量を変化させた試作したフラックス入りワイヤによる拡散性水素試験の結果を、図6に包装開封後のワイヤにおける拡散性水素量の変化を示します。先に述べたように、シームレスフラックス入りワイヤは製造時の高温脱水素処理によって、例えば全姿勢溶接用のSF-1の場合、ワイヤの全水素量は15ppm以下まで低減し、これによって拡散性水素量は2~3ml/100gと極めて低水素な溶着金属が得られます。
また包装開封直後から1カ月間において拡散性水素量に変化が無く、ワイヤ保存環境(輸送中も含め)による吸湿の影響が無いことが分かります。
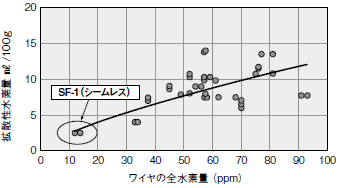
図5 フラックス入りワイヤの全水素量と拡散性水素量の関係
(JIS Z 3118 鋼溶接部の水素測定方法)
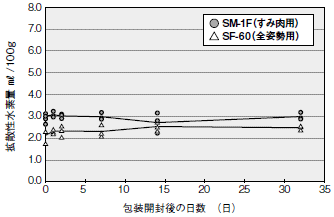
図6 包装開封後のシームレスフラックス入りワイヤにおける拡散性水素量の変化
図7に、耐低温割れ性に及ぼす拡散性水素量の影響(板厚32mm-U形溶接割れ試験結果)を示します。低温割れの発生因子としては、(1)溶接金属の硬さ、(2)溶接継手の拘束の大きさ(残留応力)、(3)溶接部の水素量が有り、この試験結果からも、拡散性水素量が低いほど割れ発生率が低減することが分かります。今後、溶接部材の高強度化や極厚化により前記(1)および(2)の因子が厳さを増す中で、シームレスフラックス入りワイヤ最大の特長である「低水素」は、一層重要な特性になっていくと考えられます。
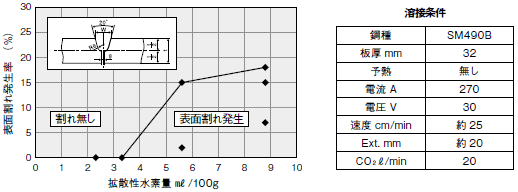
図7 耐割れ性に及ぼす拡散性水素量の影響
(JIS Z 3157 U形溶接割れ試験)
5. 最後に
近年、溶接構造物の高強度化、低温化に伴い、溶接部の要求特性もさることながら、溶接品質に対する信頼性が強く求められるようになっています。これまで培ってきたシームレスワイヤならではの高品質性に一層磨きをかけ、ユーザーの皆様が安心してお使いいただける溶接材料を提供してまいります。また、今年4月に2008国際ウエルディングショー(大阪)が開催され、新しいシームレスフラックス入りワイヤの出展を予定していますので、当社ブースへのご来場をお待ち申し上げております。