技術情報溶接Q&A
F069ホットワイヤ2電極プラズマ溶接法の開発とその適用
1. はじめに
プラズマ溶接の中には、プラズマアーク熱を用いて溶接材料を溶かし溶着量を増加する溶接法があります。これは主に以下の場合に適用します。・アンダーカットが発生するような速度での突合せ溶接を行う
・適応板厚を超えた母材を1パス溶接する
・すみ肉溶接時にのど厚を確保する
・重ねすみ肉溶接での溶接速度の高速化、施工条件難易度緩和、のど厚の確保
・肉盛溶接やフレア溶接を行う
従来のプラズマ溶接法では、ワイヤと母材の溶融をアーク熱単体で行わなければならないため、特に肉盛溶接などの高溶着量が必要な溶接では不利でした。
高溶着量が得られる方法として、ワイヤを通電加熱しながら溶融プールへ挿入するホットワイヤ溶接法(図1)があります。しかし、この従来方法には以下のような弱点があり、大幅な溶着量向上や高速溶接は望めませんでした。
・トーチの横からワイヤを挿入するという形態をとっているため、磁気干渉やワイヤ挿入位置の変動があり、溶接安定性に欠ける
・トーチの大きさや構造の関係で、アークの熱量に限界がある
また、シングルアークであることによる熱量の制限から、太い径のワイヤ(3.2mm)を用いることができず、溶接能率の向上、材料費の低減などに制約がありました。
これらの課題を克服し、高能率の肉盛溶接や高速重ねすみ肉溶接を可能にした「ホットワイヤ2電極プラズマ溶接法」を開発しましたので紹介します。
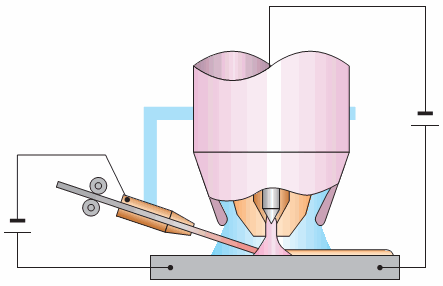
図1 従来のホットワイヤ溶接法
2. 原理と特長
ホットワイヤ2電極プラズマ溶接法の原理図を図2に示します。従来と異なる点は、タングステン電極が2本装着されていることと、ワイヤがトーチ中心部から溶融プールに供給されるということです。2つのアークとワイヤが発生させる磁界によってアークがワイヤに引き寄せられるので、ワイヤ溶融が加速され、ワイヤの高速溶融が可能となります。写真1は溶接中のアークとワイヤを撮影したものですが、傾斜したアークがワイヤと母材両方にバランスよく移行し、スムーズにワイヤが溶融しているのがわかります。また、ホットワイヤの給電距離を従来のトーチより長くしたことにより、ホットワイヤの抵抗発熱量が増加し、ワイヤの加熱温度が高くなっております。写真2は、ホットワイヤの温度をサーモグラフィで撮影した時の写真です。これにより得られた新方式でのホットワイヤ温度と、同一条件下での従来法(図1)の加熱温度を比較したものが図3です。同電流下でのホットワイヤ温度が従来法より高くなっていることが見て取れます。
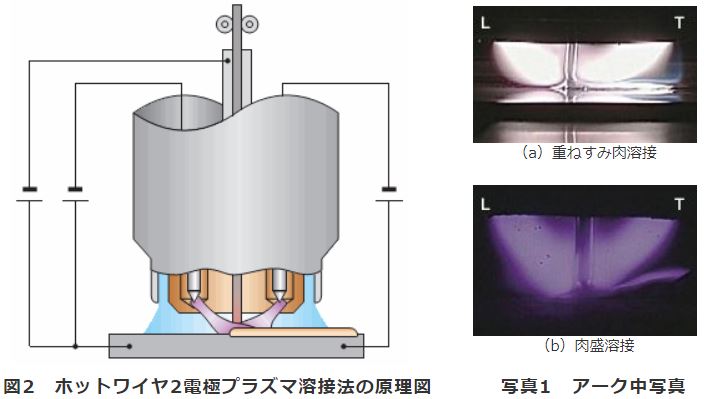
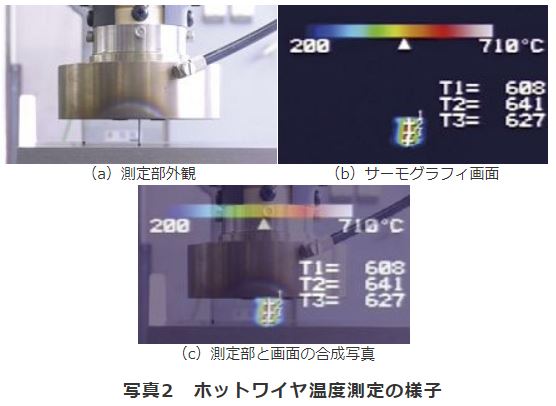
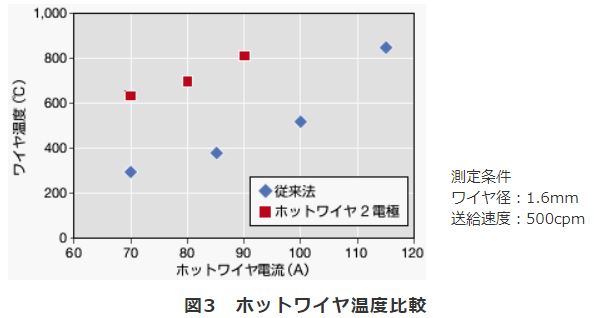
3. 構成
1)装置構成本溶接法の装置構成を図4に示します。ホットワイヤ2電極プラズマトーチ1本、プラズマ電源2台、ホットワイヤ電源1台、ワイヤ送給装置一式、トーチ冷却装置1台およびプラズマガスとシールドガスなどで構成されております。プラズマ電源には、当社のフルデジタルプラズマ溶接機、「NW-150/350AH-III」を使用します。
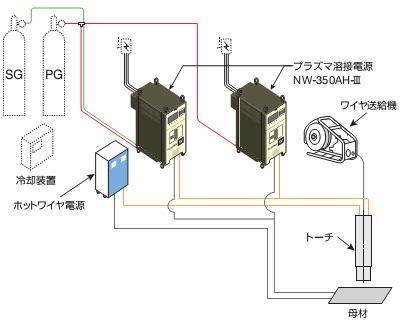
図4 ホットワイヤ2電極プラズマ溶接法の構成
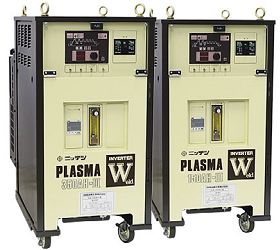
写真3 フルデジタルプラズマ電源NW-150/350AH-III
2)溶接トーチ外観
ホットワイヤ2電極プラズマ溶接トーチの外観を写真4に示します。写真のように、トーチはワイヤ矯正器や給電部などとユニット化されており、溶接治具などと接続可能なトーチホルダーも備えているため、ロボットなどへの取り付けが容易になっております。給電部は、電極棒がワイヤを左右から加圧する構造となっており、安定してワイヤに電流を供給することができます。トーチ先端には2つの向かい合ったアーク噴出孔を設けており、プラズマアークがワイヤと母材へバランスよく移行される構造となっております。
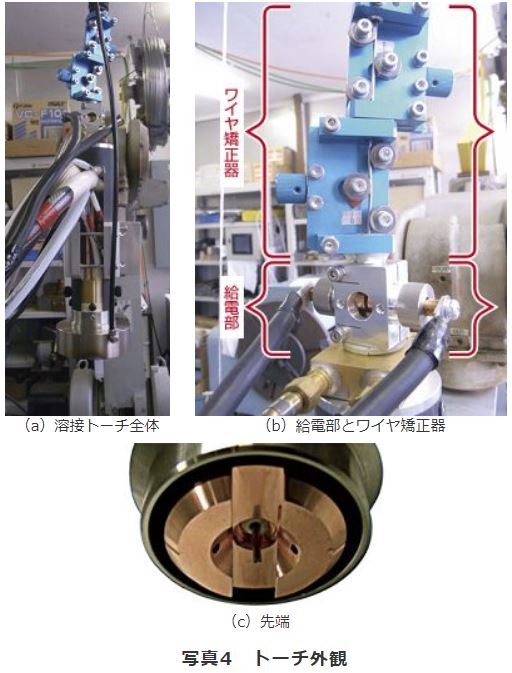
4. 適用例
写真5は、ホットワイヤ2電極プラズマ溶接を重ねすみ肉溶接に適用した場合のビード外観とマクロ断面写真です。母材にはSUS304(1.5t)を使用し、溶接姿勢は下向で行いました。なお、No.1のみ比較のために従来技術での結果を記載しております。従来のプラズマ溶接では、特にギャップのある重ねすみ肉溶接で、上板の片溶けが発生しやすいため、低速溶接が採用されておりましたが、ホットワイヤ2電極プラズマ溶接を使用することで、同等のビード外観ながら10倍(当社比)の溶接速度アップに成功しました。また、No.2(ギャップ0mm)とNo.3(ギャップ1mm)は同一条件で施工しておりますが、両者ともに良好なビード形状を得られており、ギャップ対応性の向上も見られます。
写真6は肉盛溶接のマクロ断面です。母材は全てSS400(16t)を使用しております。写真のように、1.6mmワイヤによる溝内肉盛溶接、3.2mmワイヤの適用、メタル系フラックス入りワイヤの適用を試みました。ワイヤ径1.6mmを使用したとき、従来法では300cpmの送給速度が、ホットワイヤ2電極法によると850cpmと、約3倍にアップしました。さらにワイヤ径3.2mmのものを使用すると、ワイヤ送給速度300cpmと約4倍(体積が4倍であるため)の溶着量アップに成功しました。また、メタル系フラックス入りワイヤへの適用が確認できました。
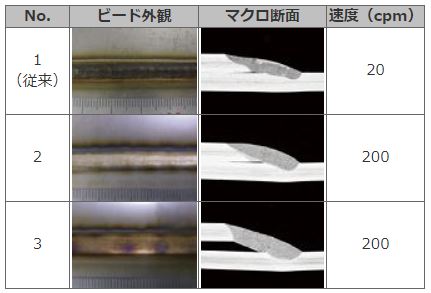
写真5 下向き重ねすみ肉溶接(SUS304 1.5t)
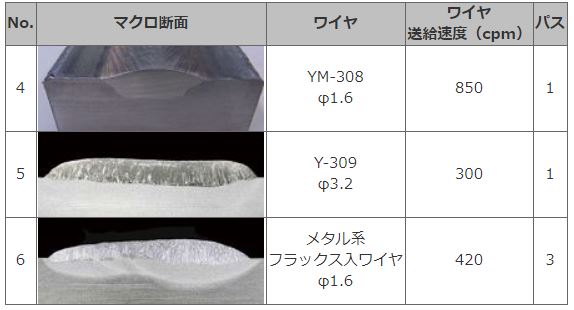
写真6 肉盛溶接(SS400 16t)
5. おわりに
ホットワイヤ2電極プラズマ溶接法という新技術を開発し、その適応について知見を得た結果を以下に示します。
1.重ねすみ肉溶接では、従来溶接速度20cpmに対して200cpmと約10倍の溶接速度が得られ、かつ開先ギャップの対応力も向上した。
2.肉盛溶接では、従来のワイヤ送給速度300cpmに対して850cpmと、約3倍の高溶着量が得られた。さらに、太径ワイヤを使用することで、溶着量を約4倍とすることも可能となった。
今後、ホットワイヤ2電極プラズマ溶接装置の早期商品化と、各材質と板厚に対する施工条件の確立を図り、生産現場での溶接や肉盛工程の大幅な能率向上、高品質化に貢献したいと思います。
1.重ねすみ肉溶接では、従来溶接速度20cpmに対して200cpmと約10倍の溶接速度が得られ、かつ開先ギャップの対応力も向上した。
2.肉盛溶接では、従来のワイヤ送給速度300cpmに対して850cpmと、約3倍の高溶着量が得られた。さらに、太径ワイヤを使用することで、溶着量を約4倍とすることも可能となった。
今後、ホットワイヤ2電極プラズマ溶接装置の早期商品化と、各材質と板厚に対する施工条件の確立を図り、生産現場での溶接や肉盛工程の大幅な能率向上、高品質化に貢献したいと思います。