技術情報溶接Q&A
F073自動車のアーク溶接部品とその溶接材料
1. はじめに
近年、自動車産業界では、環境負荷低減をテーマとしたエンジン、モータなどの原動機や、車体軽量化などの開発が進められています。車体軽量化には、アルミニウム合金、樹脂材料などの軽量素材だけではなく、高強度鋼板(以下、ハイテン)の適用による薄板化、部品形状複雑化による車体剛性向上が適用されています。薄鋼板部材には、耐食性向上のため、亜鉛めっき鋼板が使用されています。アーク溶接は、ハイテン化、部品形状複雑化による溶接継手精度の低下に対して、許容度が高いこと、溶接金属の品質が柔軟であることから、今後も不可欠な接合技術であると期待されています。
自動車のアーク溶接は、当初、炭酸ガスアーク溶接が主流でしたが、スパッタ低減、品質向上のため、Ar-20%CO₂シールドガスによる混合ガスアーク溶接の適用、さらにスパッタが多い200~300Aの中電流域では、低スパッタ(図1)、高品質化を目的としたパルスマグアーク溶接法が実用化されています。さらに低電流溶接では極低スパッタ化を実現したCMT(Cold Metal Transfer)溶接法1)、AWP(Active Wire Feed Process)制御2)が話題を呼んでいます。
本稿では、自動車部品それぞれのアーク溶接での課題とその対策、適用事例を紹介します。
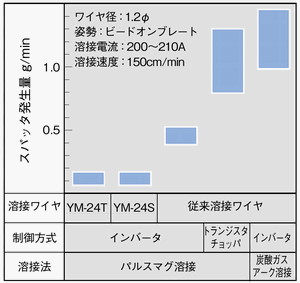
2. 自動車部品のアーク溶接の課題とその対策
自動車は、フレーム、サスペンションメンバ、ホイール、排気系部品など、目的、板厚、構造が異なる部品の集合体です。そのため、安全性、生産性向上など種々の問題があります。そこで、自動車部品ごとのアーク溶接の課題とその対策を表1に示します。表1 自動車部品ごとのアーク溶接の課題とその対策(適用事例)
自動車部品 | 代表鋼種・板厚 | 課題 | 対策 ※1 | ||
方案 | 溶接法 | 溶接ワイヤ適用例 | |||
フレーム | 軟鋼~590MPa級鋼 2.0~5.0mm |
①横向姿勢での高速溶接 :100~150cm/min ②継手精度:ビード幅、架橋性 |
①パルスマグ デジタル電源適用 ②ビード幅:YM-24S 架橋性:YM-24T |
パルスマグ マグ |
YM-24S YM-24T YM-28S |
CO₂アーク | YM-26 | ||||
サスペンションメンバ | 軟鋼~780MPa級鋼 1.5~3.0mm |
①亜鉛めっき鋼板:気孔欠陥 ②継手精度:架橋性 ③スパッタ低減 |
①パルスマグ、CO₂アーク ②YM-24T ③パルスマグ適用 |
パルスマグ | YM-22Z YM-24T |
CO₂アーク | YM-28 | ||||
ロアアーム アクスルビーム |
軟鋼~590MPa級鋼 2.5~4.0mm |
①ハイテン化 ②架橋性 ③溶込みの安定化 |
①安定した溶接継手性能 ②YM-24T ③溶接条件の選定 |
パルスマグ マグ |
YM-24T YM-28S |
CO₂アーク | YM-28 | ||||
アクスルハウジング | 軟鋼~490MPa級鋼 3.5~6.0mm |
①高速溶接 :100~150cm/min ②フラットな溶込み形状 ③溶込みの安定化:耐リーク性 |
①パルスマグ デジタル電源適用 ②YM-24S ③溶接条件の選定 |
パルスマグ マグ |
YM-24S YM-24T YM-28S |
CO₂アーク | YM-26 | ||||
ホイール | 軟鋼~590MPa級鋼 2.0~5.0mm |
①ビード外観:耐リーク性 ②スパッタ低減 ③疲労強度 |
①溶接条件の選定 ②パルスマグ ③応力集中緩和(溶接条件) 圧縮残留応力 SM-10N |
パルスマグ | YM-24T YM-28 |
CO₂アーク | YM-28 SM-10N |
||||
トルクコンバータ | 軟鋼~490MPa級鋼 2.0~4.0mm |
①耐リーク性 ②スパッタ低減 |
①溶接条件の選定 ②パルスマグ |
パルスマグ | YM-24T YM-28 |
CO₂アーク | YM-28 | ||||
インパネフレーム シートフレーム |
軟鋼~490MPa級鋼 0.8~2.0mm |
①ビード外観:溶落ち ②スパッタ低減 |
①低電流、細径ワイヤ CMTなど ②低電流、細径ワイヤ プラズマなど |
CO₂アーク マグ (CMTなど) |
YM-28 YM-25 YM-24T YM-SCM |
ボディ、ピラー ドアフレーム |
0.6~1.4mm軟鋼~ 780MPa級鋼 |
プラズマ | |||
エキゾーストマニホールド マフラー |
フェライト系ステンレス鋼 SUS430、SUH409など 0.5~5.0mm |
①耐食性:鋭敏化 ②ビード外観:溶落ち ③低スパッタ化 |
①極低C、Nb添加ワイヤ ②低電流、CMTなど ③プラズマ、パルスミグ |
パルスミグ (CMTなど) |
YM-160 FCM-430NL |
プラズマ |
●2.1 フレーム
フレームの溶接は、横向姿勢で高速溶接であること、厚板・ハイテン材を使用することからスプリングバックによる継手精度の低下が課題とされ、幅広なビード形状、架橋性(板隙、GAP)が要求されます。
パルスマグ溶接法は、高能率な高速溶接および、ピーク電流での予熱効果によるハンピングのない健全な溶接ビードが得られます。
YM-24S×パルスマグ溶接は、横向姿勢において(図2)、幅広なビード形状、また良好な架橋性が得られます。
YM-24T×パルスマグ溶接は架橋性が良好(図3)です。
従来、YM-26×炭酸ガスアーク溶接は、安定した溶接金属性能が得られるため、採用されています。
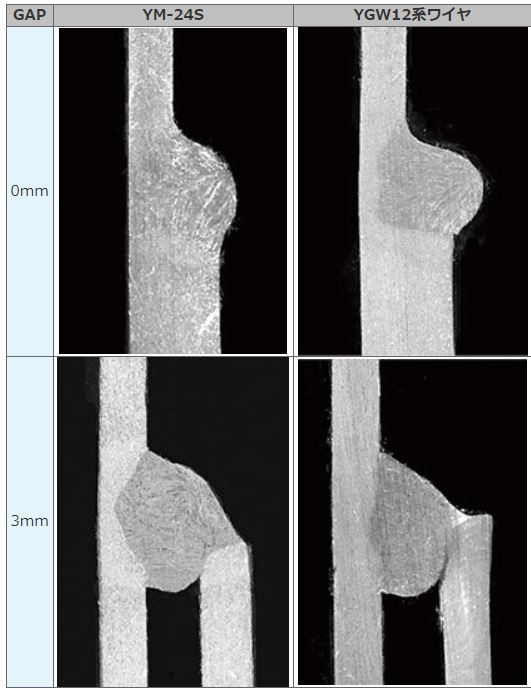
図2 横向姿勢におけるパルスマグ溶接での溶接ビード断面マクロ
(普通鋼板:2.9mm、横向重ねすみ肉、250A-25V-100cm/min)
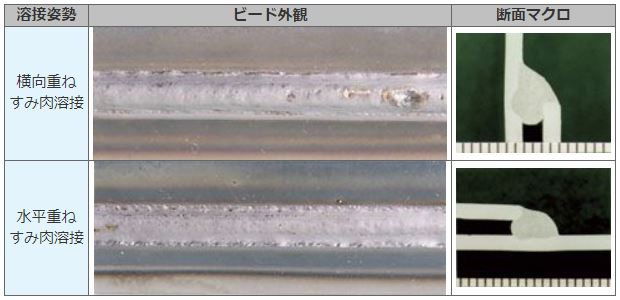
図3 YM-24Tのパルスマグ溶接における溶接ビード外観と断面マクロ
●2.2 サスペンションメンバ
サスペンションメンバは、足回り部品でも特に路面に近いことから、耐食性が要求され、亜鉛めっき鋼板が一般的に採用されています。そのため、ピット・ブローホールなどの気孔欠陥、スパッタ発生、ハイテン化と複雑な部品形状による継手精度の低下も課題です。
YM-22Z×パルスマグ溶接は、ワイヤ化学成分とパルスの溶融池振動によるガス抜けの相乗効果により、気孔欠陥を低減(図4・5)すること、スパッタ低減(図6)が期待できます。
YM-24T×パルスマグ溶接も、亜鉛めっき鋼板で気孔欠陥の少ない良好なビード(図5)が得られ、またスパッタ低減にも効果があります。架橋性も良好(図3)なため、採用されています。
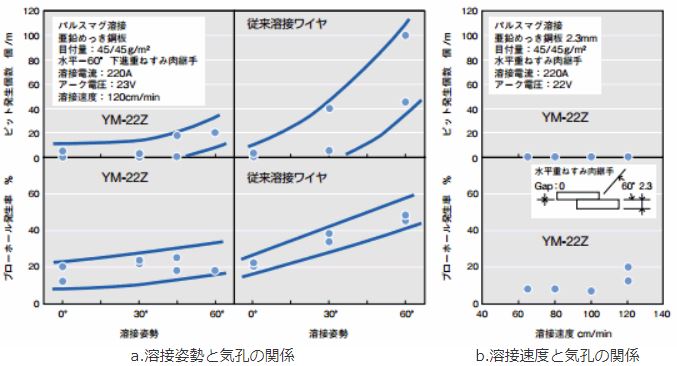
図4 YM-22Zの溶接姿勢と気孔発生の関係および溶接速度と気孔発生の関係
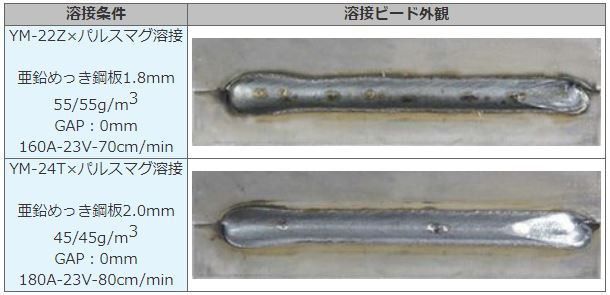
図5 亜鉛めっき鋼板のパルスマグ溶接におけるビード外観
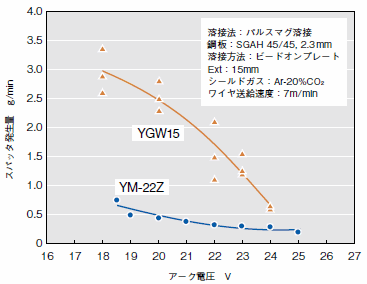
図6 YM-22Zのパルスマグ溶接でのスパッタ発生量
●2.3 ロアアーム、アクスルビーム、アクスルハウジング
ロアアーム、アクスルビームおよびアクスルハウジングなどの足回り部品の課題は、ハイテン化などによる架橋性、溶込み安定化です。
ロアアーム、アクスルビームは、YM-24TやYM-28S×パルスマグ溶接では、溶込みが良好なため、適用されています。
アクスルハウジングは下向姿勢での高電流溶接が行われています。YM-24S×パスルマグ溶接は幅広で、フラットな溶接ビード形状(図7)が得られるため、採用されています。またYM-26×炭酸ガスアーク溶接も適用されています。
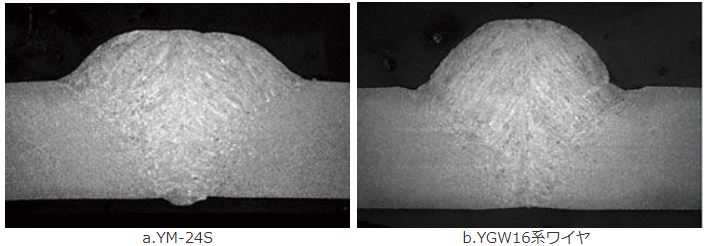
図7 YM-24Sの断面マクロ
(板厚:4.2 mm、突合、260A-29V-120cm/min)
●2.4 ホイール、トルクコンバータ
ホイールとトルクコンバータの用途は全く異なりますが、円周溶接を行うことや、溶接に対する要求品質は類似しています。
ホイールの溶接は低スパッタ化、ビード外観、リム内の溶接では耐リーク性が課題です。そのため、高品質なパルスマグ溶接が主流となっています。ホイールは自動車走行時、回転と路面の凹凸の影響を受け、複雑な振動が加わるため、疲労破壊のリスクが高いです。対策として、ビード形状改善による応力集中の緩和と、低温変態溶接材料SM-10Nによる圧縮残留応力の付加が挙げられます。
トルクコンバータは、オイル漏れ防止のため、耐リーク性が課題で、安定したパルスマグ溶接、炭酸ガスアーク溶接が行われています。
●2.5 インパネフレーム、シートフレーム、ボディなど
インパネフレーム、シートフレームは、自動車部品の中でも、特に薄鋼板が使用されており、溶落ち低減によるビード外観の向上、スパッタ低減が課題です。そこで、短絡(ショートアーク)溶接が採用され、YM-28、YM-25などが使用されています。
また、シートフレーム、ボディの溶接にCMT溶接法がYM-28、YM-24Tの0.9~1.2Φとの組合せで使用されています。一方、プラズマアーク溶接もボディのテーラードブランク溶接を中心に多種多様の部品に適用されています(図8・9)
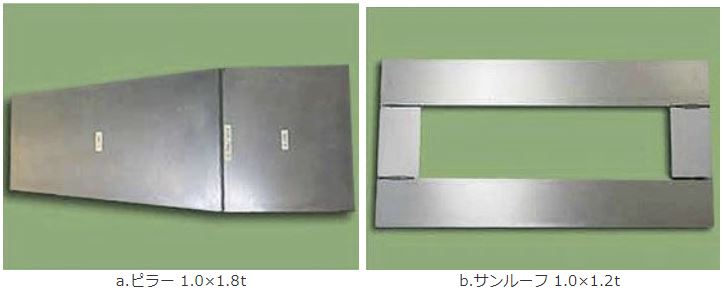
図8 プラズマアーク溶接でのテーラードブランク溶接部品の溶接試験体
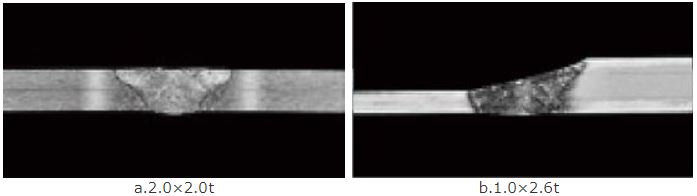
図9 プラズマアーク溶接でのテーラードブランク溶接の断面マクロ
●2.6 エキゾーストマニホールド、マフラー
排気系部品であるエキゾーストマニホールドやマフラーは、軽量化と高温での耐酸化性が求められ、SUS430、SUH409などフェライト系ステンレス鋼が主流となっています。溶接部では鋭敏化が大きな課題であり、溶接材料には極低C、Nbの適正添加をしています。
当社では、鋭敏化に優れたミグ溶接用YM-160(ソリッドワイヤ)、FCM-430NL(メタル系フラックス入りワイヤ)をラインナップしています。パルスミグ溶接との組み合せで、ビード外観(図10)、耐食性(図11)は良好で、低スパッタ溶接が得られます。
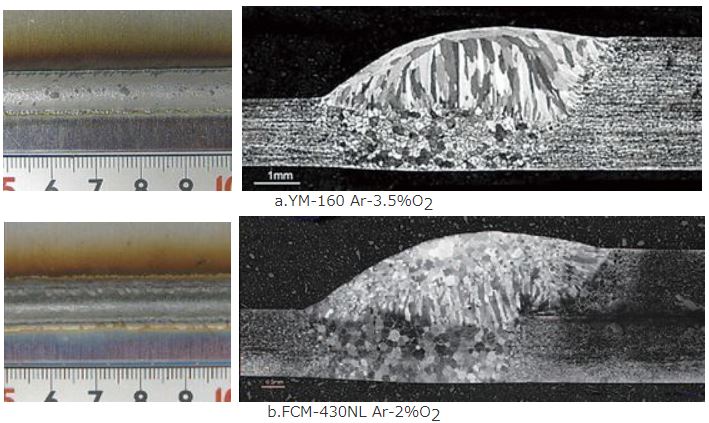
図10 フェライト系ステンレス鋼の溶接ビード外観および断面マクロ
(パルスミグ溶接、120A-22V-80cm/min)
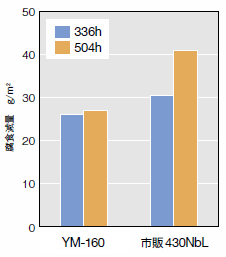
図11 フェライト系ステンレス鋼溶接試験体の塩水噴霧試験結果
(JIS Z2371 試験温度:35℃)
3. おわりに
自動車部品とそれぞれのアーク溶接の課題と対策について紹介しました。読者各位におかれましては、本稿および当社製品の活用による安全で安心な品質、かつ低コストなものづくりの一翼を担えれば幸甚です。<参考文献>
1)古川一敏:軽金属溶接.43(10),p.465(2005)
2)藤原潤司:溶接技術59(2),p.51-56,(2011)