技術情報溶接Q&A
F086プラズマ溶接のメリットについて
1. はじめに
当社のプラズマ溶接事業は、ミネベア(株)殿が約40年前の1974年にプラズマ溶接機の販売を始めたことにさかのぼります。約30年前の1984年に旧日鐵溶接工業が事業を引き継ぎ、現在の国内販売のシェアはNo.1(約60%)です。
スパッタ、ヒューム、スラグが出ない、ひずみが少ない、開先加工不要などの特長を持ったプラズマ溶接ですが、溶接業界全体からすると比率はわずかです。その大きな要因はプラズマ溶接自体が一般的にはあまり知られていないことにあります。
そこで今回は、プラズマ溶接のメリットについて紹介します。
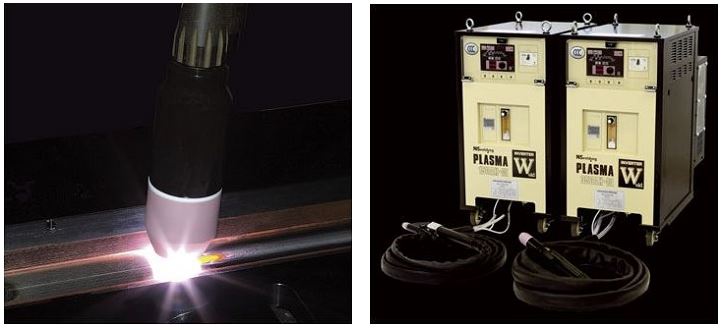
2. プラズマ溶接とは
プラズマ溶接は、電極と母材との間でアーク放電をさせる非消耗式溶接法です。TIG溶接と異なり、図1のとおり水冷ノズル内にプラズマガスを流し電極と母材間でアークを極限まで狭窄して得られるエネルギー密度の高いアーク熱源を用います。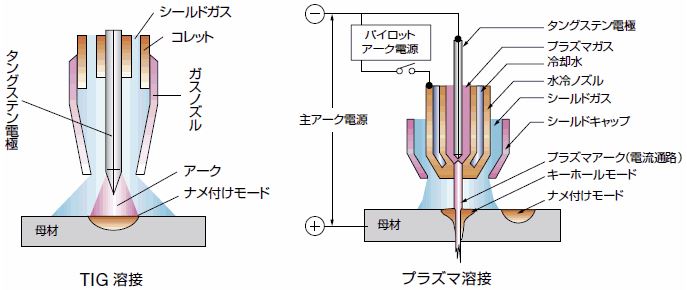
図1 TIG溶接とプラズマ溶接の比較
そしてそのプラズマガスの流量を調整することで2通りの溶接法が選べます。流量を少なくするとTIG溶接のようなナメ付け溶接、増やすと強烈なプラズマアークとなり母材を貫通させるキーホール溶接が可能となります。キーホール溶接はプラズマ溶接の最大の特長で溶込みが深く貫通力があります。
3. キーホール溶接法について
図2にキーホール溶接の原理を示します。水冷ノズルの小孔から放出される高温のプラズマガスの流量を多くすると母材溶融プールを押し分け、ついには母材を貫通して裏側に抜けます。この状態でトーチを移動すると、溶融金属はトーチ後方に回り込み溶融プールを形成、凝固しながら溶接ビードを連続的に形成します。写真1は、キーホール溶接の状態を進行方向の横側より撮ったものです。このように、裏までアークが貫通している様子がわかります。写真2は、SUS304での溶接前の継手形状及び溶接後のナゲット形状を示します。プラズマアークの高温ガス気流が直接突き抜けることで、鋼板の裏側へも効率良くアーク熱を作用することができ、表側よりアーク熱を照射し熱伝導のみで裏ビードを形成する一般的な溶接法に比べ、はるかに高能率な溶接が実現できます。
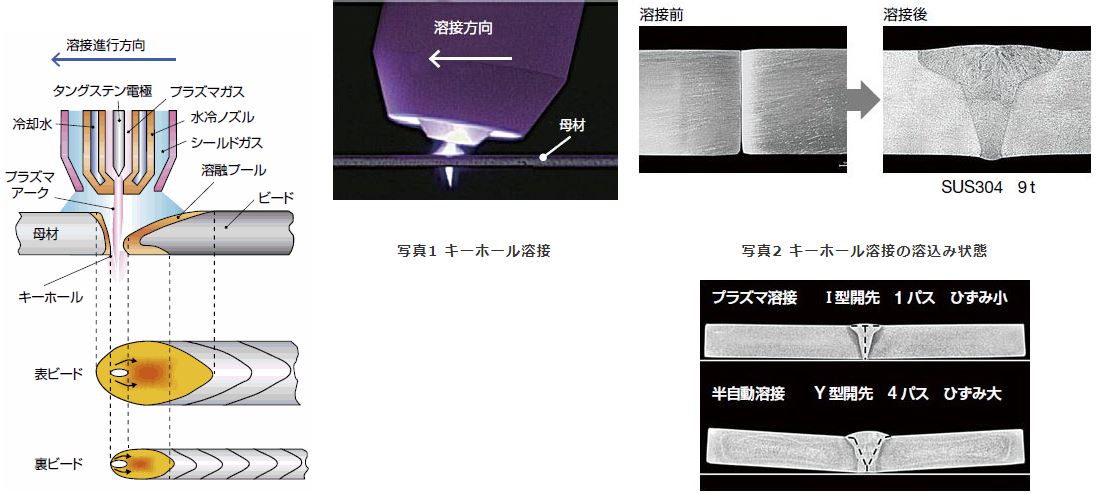
●キーホール溶接の特長をまとめると、次のとおりになります。
1)開先加工不要
開先のないI型突合せ溶接で片面より1パス溶接が可能です。適応板厚SUS3~9t・SS3~6t(0.1~3tはナメ付け溶接で対応)
2)ひずみ取りの省力化
写真3はプラズマ溶接と半自動溶接のひずみを比較したものです。
4パス溶接の半自動溶接に対して1パスで済むプラズマ溶接はひずみが少ないことがわかります。
3)自動化に最適
電極棒の消耗が少ないので長時間安定した溶接が可能となり生産性の向上が図れます。
4)コスト低減
溶接パス数を低減できるため、作業時間の低減となります。
5)後加工が安易
余盛量を適量にコントロールすることができ、ビードカットの工数削減が可能です。
6)スパッタ、スラグの発生がないクリーンな溶接
スパッタ防止剤の塗布や溶接後のスパッタ取り、スラグの処理が不要になり、クリーンな溶接が可能です。
●キーホール溶接の板厚限界(SUS9t・SS6t)以上の板厚への適用例も多くなってきています。
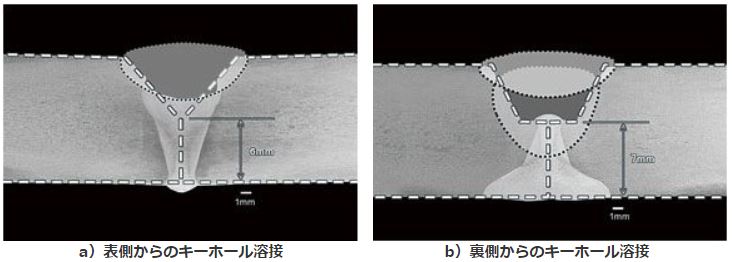
写真4 開先ルート部のキーホール溶接(SUS304,12t)
写真4は、SUS304、12tの板厚で開先ルート部をキーホール溶接で行い、その後余盛溶接を行う方法です。
a)はY形開先のルート部6㎜を表側よりキーホール溶接で行い、残り部にワイヤを供給して同じくプラズマ溶接で余盛溶接を行う方法です。
b)はU形開先のルート部7㎜を開先の反対側よりキーホール溶接を行い、残りのU形開先溝を余盛溶接する方法です。余盛溶接を他の溶接法(MIG溶接、サブマージアーク溶接)で行うこともできます。
この方法を用いると以下のような利点があります。
1)ルート部の長さを長くでき、余盛回数を少なくできます。
2)安定した裏波ビードの形成が可能です。
3)溶材の使用量を少なくできます。
4)X開先時の裏はつり工程は不要です。
4. プラズマ溶接機採用の理由
プラズマ溶接機が採用される最も多いケースは、現状MAG溶接やTIG溶接をご使用中のお客様です。下記のような課題解決を希望されています。MAG溶接の課題 | TIG溶接の課題 | |
開先加工の省略 スパッタ取り工程の省略 安定した完全フルペネ溶接の要望 ひずみ取り工程の省略など |
手動溶接を自動化したい(品質の安定と熟練工対策) 開先加工の省略 ひずみ取り工程の省略など |
表1 他溶接法とのコスト比較例
項 目 | プラズマ溶接 | MIG溶接 | TIG溶接 | |
溶接条件 | 電流(A) | 180 | 250 | 200 |
溶接速度(cm/min) | 28 | 40 | 15 | |
エッジ処理 (開先形状) |
![]() |
![]() |
![]() |
|
ワイヤ使用量(g/m) | なし | 300 | 300 | |
層数(pass) | 1 | 2 | 3 | |
所要時間(min) | 3.6 | 5 | 20 | |
ランニングコスト | 開先加工費 | ─ | ─ | 150 |
電力代 ¥20/kwh | 17(13.8kw) | 24(14.4kw) | 53(8kw) | |
Ar ガス ¥0.70/L | 25(10L/min) | 53(15L/min) | 140(10L/min) | |
H2 ガス ¥0.30/L | 2(2L/min) | ─ | ─ | |
材料費 ¥2,000/kg | ─ | 700 | 600 | |
工賃 ¥50/min | 180 | 250 | 1,000 | |
合 計(¥/m) | 224 | 1,027 | 1,943 |
5. 適用例
薄板の突合せ溶接で、キーホール溶接を採用して効果を上げ、広く使用されているワークの代表例をあげます。(1)食品またはケミカルタンク(SUS3~9t)(写真5)
食品またはケミカルタンクに適用されるプラズマ溶接機の利点は、①開先加工が不要で、片面よりワンパスフルペネの溶接が可能、②ひずみが少なく、ひずみ取り工程の削減や省略が可能、③自動溶接が可能で溶接熟練工でなくても美しいビード仕上がりで後行程が容易、などがあげられます。これらの利点により行程の高能率化やコスト削減が図れることから、MIG溶接やTIG溶接に替わり広く適用されています。
(2)エアコン用圧縮器ケースのシーム溶接(SPCC2.6~5t)(写真6)
エアコン用圧縮器ケースのシーム溶接へ適応される利点では、①ワンパスフルペネの溶接ができる、②自動溶接で長時間安定した溶接が可能、③スパッタ取りが不要、④裏ビードカット行程が不要(裏ビードを凹み形状にコントロール可能)、などがあり、各エアコンメーカー殿で広くご使用いただいています。
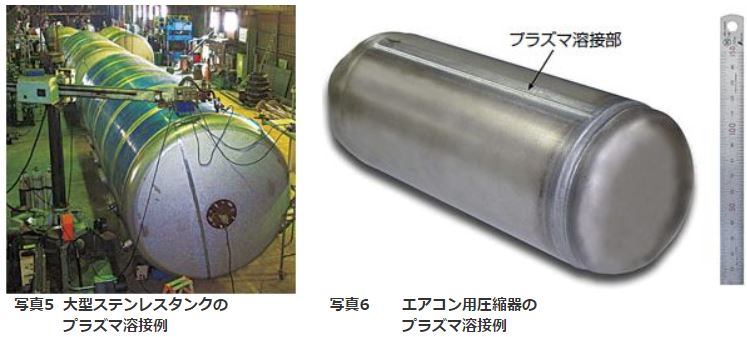
そのほかにも自動車のサスペンション部品やステンレスパイプの連続造管ラインなど、キーホール溶接は炭素鋼板やステンレス鋼板を問わず広く利用されています。
6. 高速溶接ができる2電極プラズマW-PLASMAの紹介
高能率が強みのプラズマ溶接ですが、それでもレーザー溶接に対しては速度で劣ります。理由は適正な溶接速度を超えると表ビード両端部にアンダーカットが発生してしまうためです。
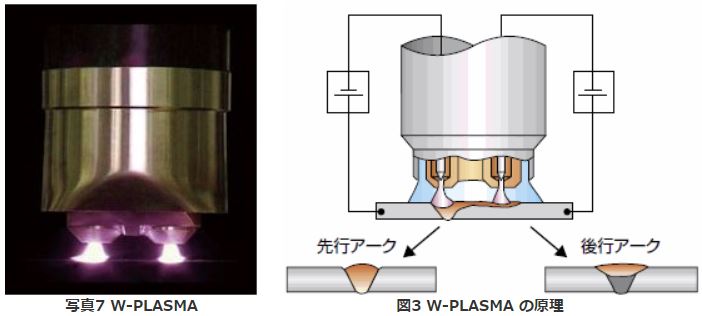
そこで開発されたのが写真7の2電極プラズマ溶接法(W-PLASMA)です。図3のとおり1つのトーチに2つのプラズマアークを近距離で発生させて先行プラズマアークでキーホール溶接を行い、後行プラズマアークで先行極で発生したアンダーカットを平滑化する方法です。これにより高速溶接でもアンダーカットの極めて少ない溶接となり、従来の1電極プラズマ溶接に比べ約2倍の高速化が図れます。
7. 亜鉛めっき鋼板に最適DS(ダブルシールド)-PLASMAの紹介
亜鉛めっき鋼板は溶接すると、表面の亜鉛が溶接時の熱によりガス化し亜鉛ヒュームが発生します。これまで亜鉛ヒュームはプラズマ溶接トーチに付着堆積するため繰り返し溶接を行った時に溶接が不安定になる問題がありました。
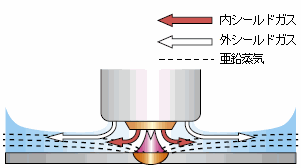
図4 亜鉛めっき鋼板溶接の原理図
この問題に対して当社では、DS-PLASMA溶接法を提案しています。DS-PLASMA溶接は図4のとおりトーチ先端が二重構造となっています。内ノズルより流される流速の速い内シールドガス流で亜鉛ヒュームをトーチの外側へ押し出し、さらに外ノズルから流されるシールドガス流で、遠方へ押し流すことで、トーチ先端部への亜鉛付着量を減少させる溶接法です。これによりトーチの消耗品が従来よりも長寿命になります。メンテナンス回数を減少させることができるため長時間安定した溶接を行うことが可能です。
8. 自動溶接装置
プラズマ溶接は高速で長時間安定した溶接が可能なため、何らかの装置と組み合わされることが多くなります。装置の構造としては大別すると、トーチが走行する方式とワークが走行する方式の2方式があります。トーチが走行する方式としては、ロボットや自走台車、クランプシーマ、マニプレータ装置などがあります。写真8はステンレスタンクのシーム溶接に使用されるクランプシーマ溶接装置で、写真9は円錐型鏡板の溶接もできる新製品の吊り下げ式簡易型シーム装置です。
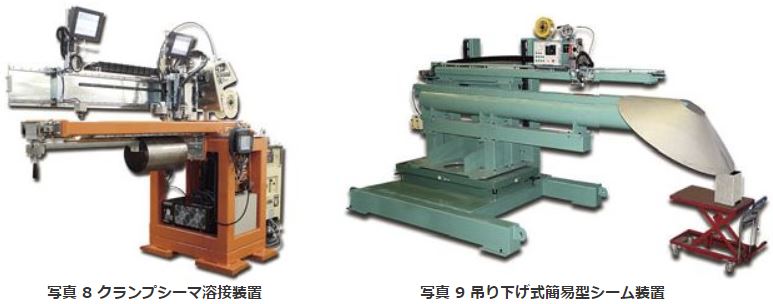
もう一方のワークが走行する方式としては、エアコン用圧縮器ケースのシーム溶接(写真5)に使用されるトンネル型パイプ製造機(短管)や連続造管ライン(長尺管)などがあります。
このようにプラズマ溶接機は、さまざまな自動装置と組み合わせて使用されることで、その特長を発揮し生産能率の向上に寄与しています。
9. プラズマ粉体肉盛溶接
プラズマアークは熱集中度が極めて高く、この高温プラズマアーク中に粉末を供給し、粉末を溶かしながら肉盛金属を形成する溶接法がプラズマ粉体肉盛溶接法です。粉体はアルゴンなどのキャリアガスによって供給され溶接トーチに達し、プラズマアーク中に挿入され、その後溶解、母材に溶着されます。
肉盛溶接で要求される品質項目はビード形状、余盛量、希釈率、粉体歩留ですが、熱源としてのプラズマ溶接電流、溶込み深さ制御のプラズマガス流量と粉体の供給量を別々に制御することができるので、希釈率、余盛量、ビード形状のコントロールが容易です。ほかの溶接法と比較するとプラズマ溶接ではアーク長が長く高温であることと、粉体の表面積が大きいことから粉体を効率良く溶融することができます。粉体の歩留が良く、また溶加材と被溶接材は低希釈ではありますが合金化しているので耐衝撃性も高くなるため、エンジンバルブのような耐熱、耐摩耗性、耐衝撃性を求められる分野をはじめとし、各分野で幅広く使用されています。
10. おわりに
以上、プラズマ溶接につきまして紹介しましたが、いかがでしたでしょうか。本件に関するお問い合わせやプラズマ溶接について興味をもたれた方がいらっしゃいましたら、当社各支店またはプラズマ事業部へご相談ください。また、プラズマ溶接につきましては、基本的な内容を記載したカタログ『知っていますか?プラズマ溶接』という冊子も作りましたのでご希望の方は同様にご依頼ください。